While it is quite common to use various different geometries for the electro-slag remelting process which is relatd to the VAR process, it is still common to use cylindrical geometries for the VAR process alone. A remelting closer to the final dimension could e.g. provide potential savings in energy and subsequent process costs. Due to the difficulties caused by the process in investigating the process and the very high quality requirements at the same time, such a change in process control, which is associated with many parameter and geometry changes, is difficult to achieve using experimental methods and is also associated with enormous costs. Through the improvement of computer technology and simulation software, the possibility of achieving a greater innovation boost for such processes, which are difficult to access from the outside, through process simulations is becoming more and more probable.
The IOB, which is specialized in the model-based analysis of thermal processes in metallurgy, is interested in the generation of innovative further development possibilities of the VAR process to transfer similar advantages of the different variants of the ESU process to the VAR process. Based on an existing 2D VAR model for the investigation of axially symmetric geometries, a 3D model was developed which allows the mapping of the VAR process in rectangular geometries.
The existing model is based on a 3 model coupling of electromagnetic FEM calculation, thermoelastic FEM and CFD calculation to approximate the various phenomena in the VAR process.
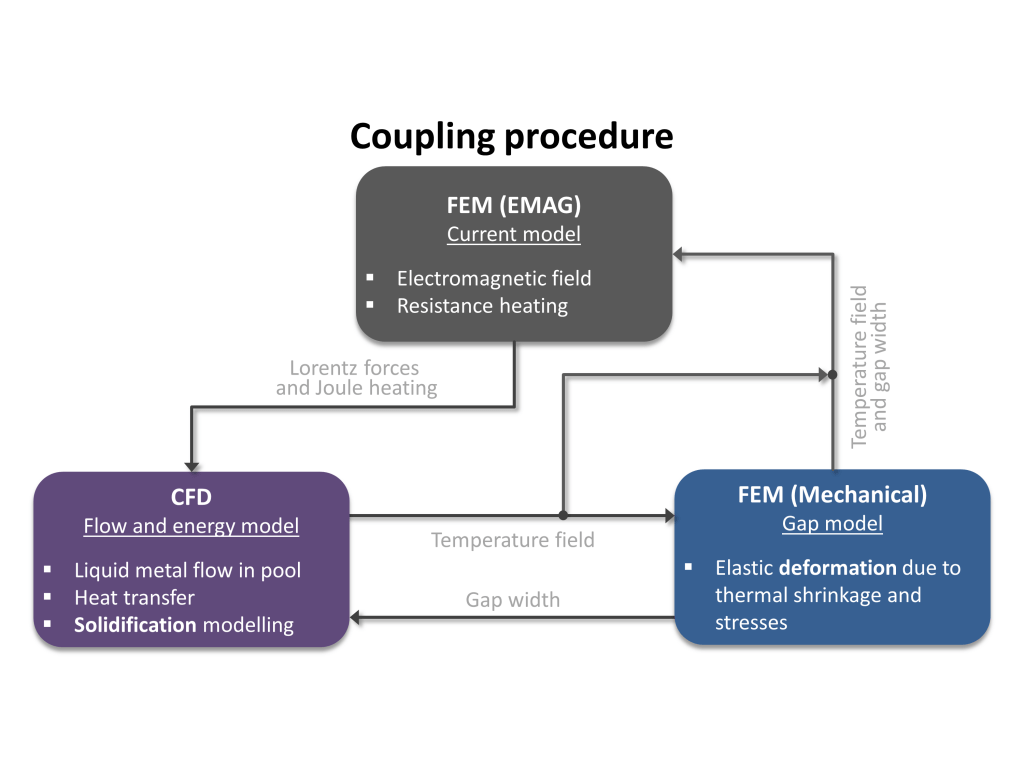
This allows conclusions to be drawn about the solidification and flow behaviour in the metal pool. This is particularly important for the material properties to be adjusted and enables initial conclusions to be drawn about the effects of a changed process geometry.
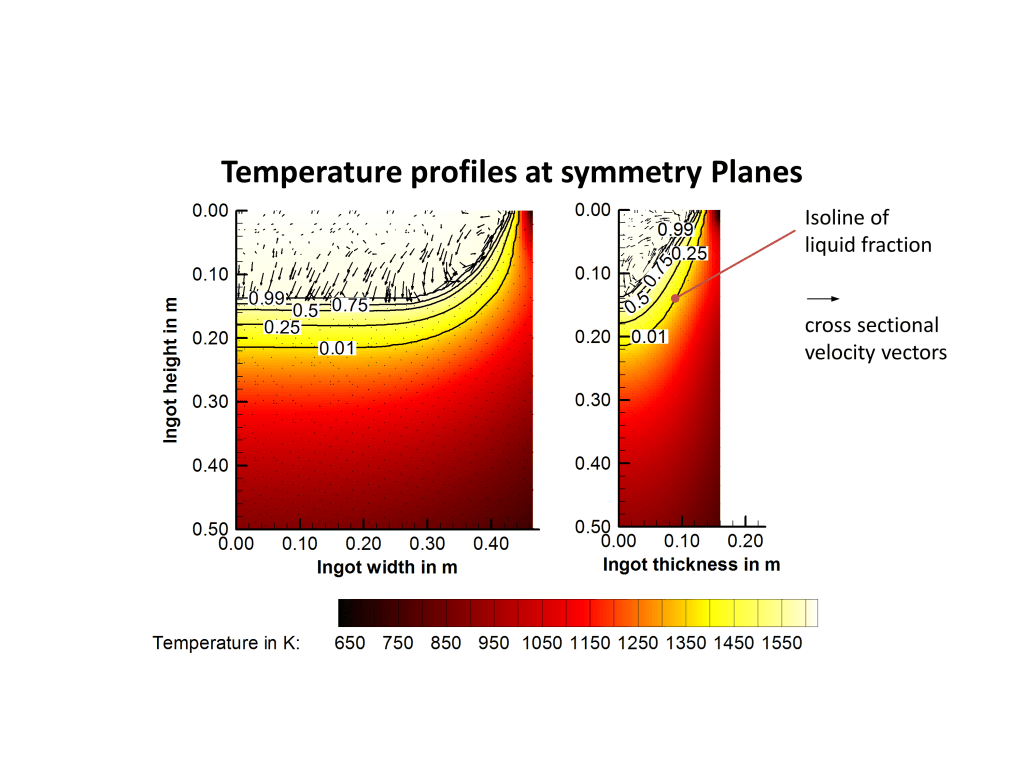