Numerical modeling of the momentum, heat and mass transfer in the Vacuum Arc Remelting process
Vacuum arc remelting (VAR) is a refining process for the production of high-purity metallic materials. It uses a very pure electrode made of material of its own type, which is often melted in a vacuum induction furnace and refined in the electroslag remelting process.
The VAR system essentially consists of a water-cooled copper mould and a power supply to which the electrode to be remelted is attached. A voltage is applied so that electrical discharges take place between the electrode and the block. The energy released is used to melt the underside of the electrode. After mass transfer in the form of metal droplets, a metal pool forms in the mould, which solidifies continuously towards the edge.
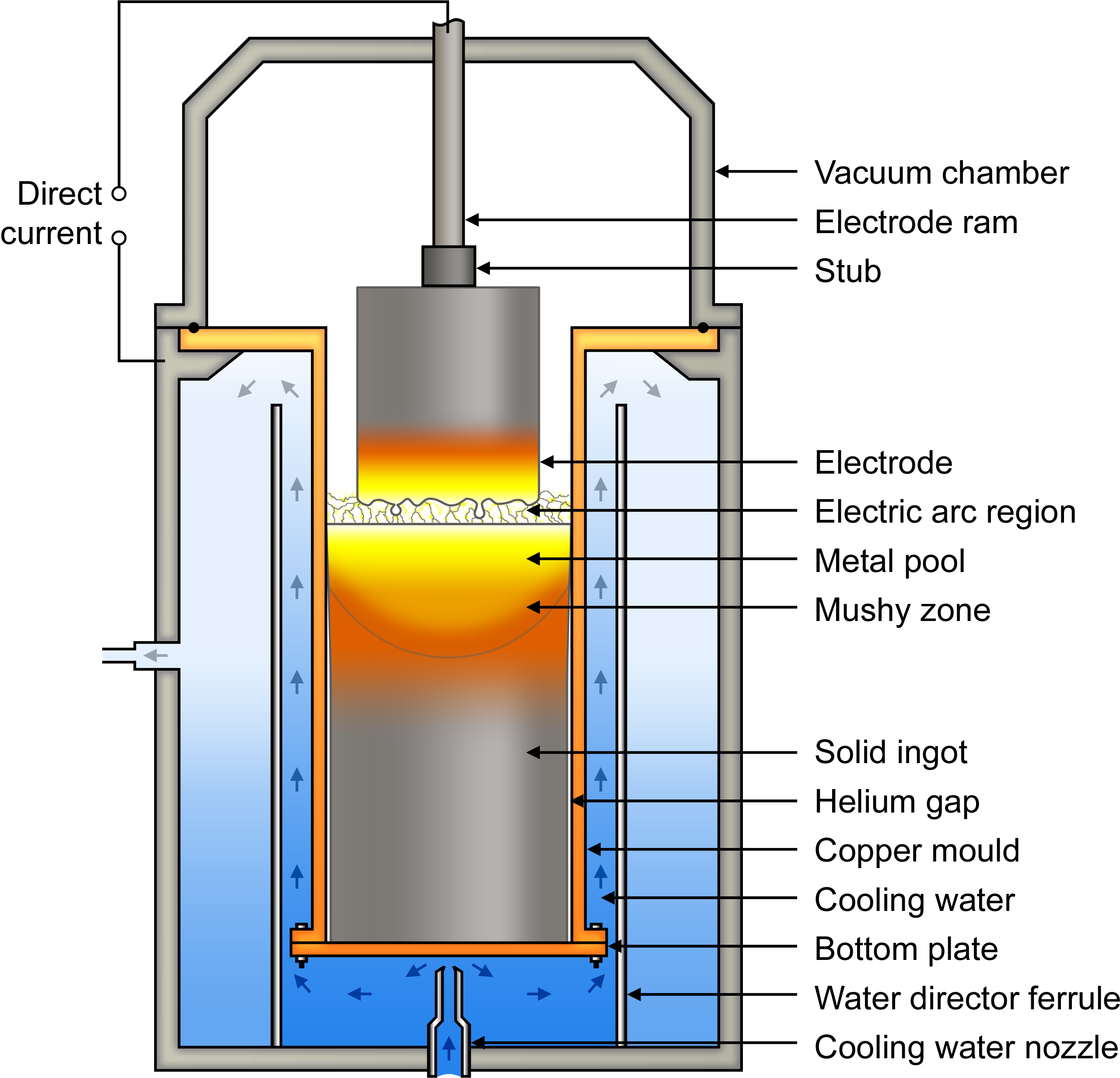
The refining effect is based on the high vacuum surrounding the electrode. In combination with the small metal droplets and the large diffusion coefficients at high temperatures, dissolved gases can be extracted from the metal. A further goal of the process is the production of a controlled directional solidification structure with low segregation.
The process is very time-consuming and expensive, which is why it is only used for high-quality steels, titanium, zirconium and nickel superalloys. The materials produced in this way are used in tool making, the chemical industry as well as in the aerospace industry. The extreme requirements in these applications require a high degree of process knowledge and control.
In cooperation with VDM Metals GmbH, the VAR process is numerically investigated at the IOB. The simulation of flow, heat balance and solidification is able to simulate the shape of the metal pool, which is a decisive quality characteristic of a known process. Thus, the resulting pool profile can be calculated with the model even with slightly changed process parameters.
The validation of the model is based on metallurgical micrographs of samples from the real process. The microstructures were made evaluable according to the “macroscopic microstructure image” method. Using a MATLAB program, the shape of the metal pool is reconstructed from the growth directions of the dendrites, which can be compared with the simulation.
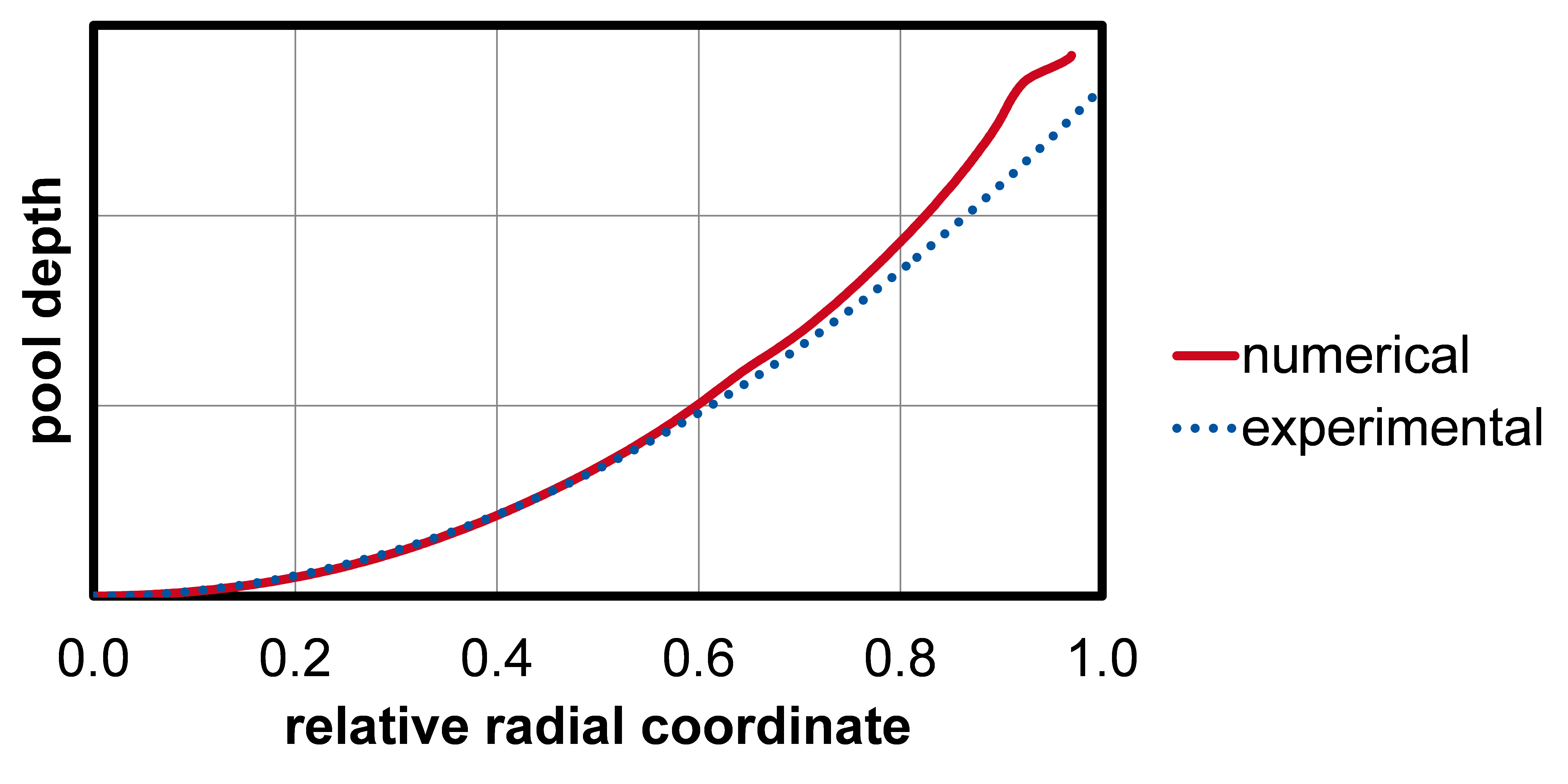