Combustion and Burner Technologies
Contact person: Dr.-Ing. Nico Schmitz
Fields of activities
Combustion technology and energy efficiency, hydrogen, flameless combustion, flow and combustion simulation, process gas and off-gas analysis
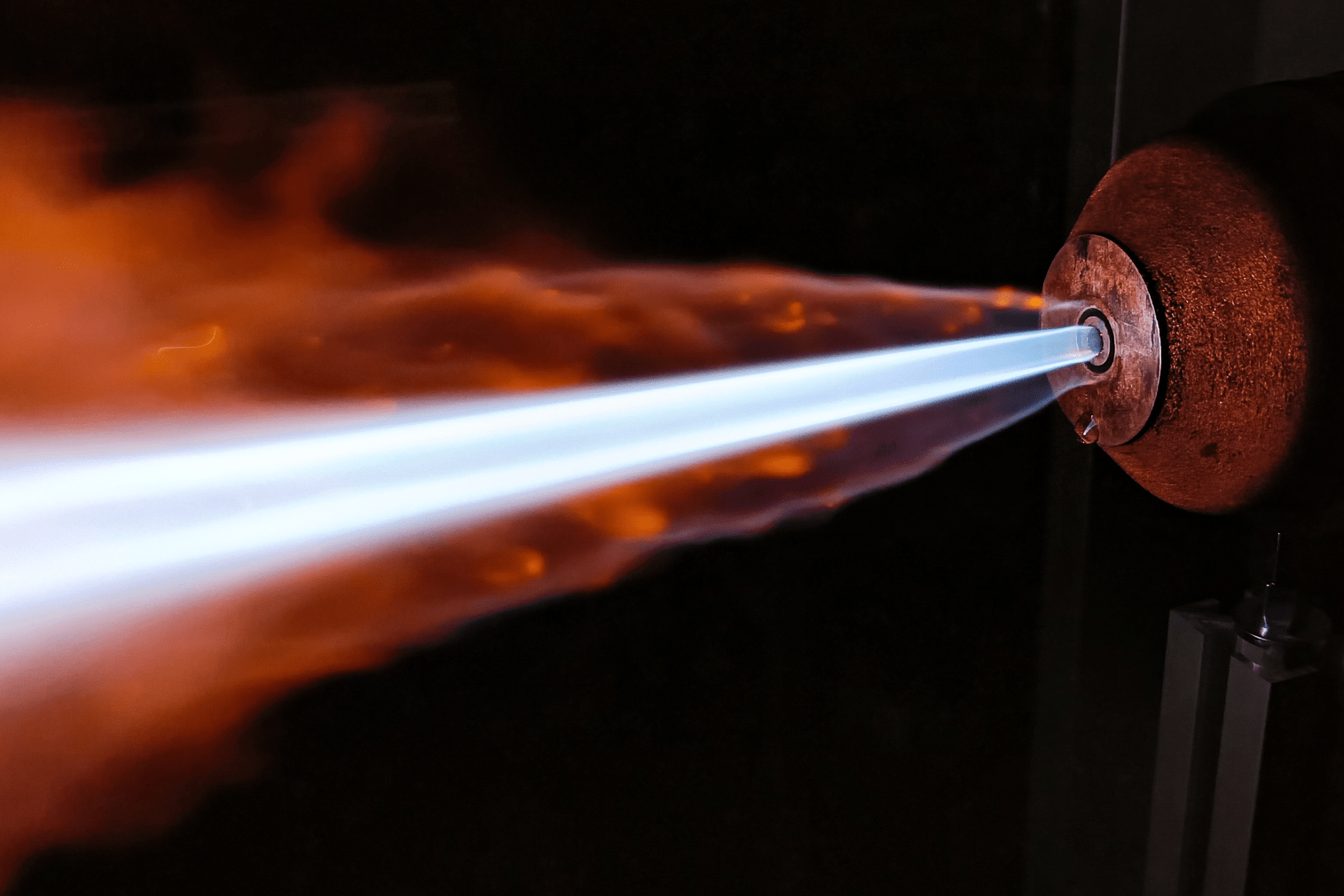
Areas of research
Low-carbon fuels
The core activities in this area are the research and development of technologies and processes for the use of low-CO2 fuels such as hydrogen in thermoprocessing plants. We aim to support and drive development ranging from conception, numerical simulation, and experimental studies on a pilot scale to implementation and demonstration in industrial plants.
For this purpose, various test furnaces for burners are available (max. burner capacity approx. 250 kW). These can be supplied with high calorific natural gas, hydrogen and any mixtures of other cylinder gases (N2, CO2, CO, CH4, C3H8, NH3, O2) via a versatile gas mixing infrastructure. In addition, a powerful in-house computational infrastructure is available to carry out CFD simulations and modelling activities, supplemented by a connection to the RWTH Compute Cluster for even the most complex numerical models.
Extensive investigations are carried out in the test furnaces, including flow and temperature measurements (conventional, non-contact, suction pyrometer). Additionally, process gas/off-gas analysis and flame characterization by means of OH* spectroscopy are available. In many cases, the measurements also serve to validate the numerical models built up in-house, enhancing confidence in simulations for scale-up applications.
Ultra-low NOx combustion technology
Low NOx combustion processes have been investigated at IOB for many years. The focus lies on extending the application limits of flameless combustion (FLOX) for small and large burner capacities and new fuels. The development of multi-stage flameless oxidation (FLOX‑2) is an innovative extension of this field of work.
This is enabled by the use of a particularly accurate process gas analysis system, which has been optimized from sampling to analysis for lowest NOx concentrations. Our group has many years of experience carrying out complex measurement tasks in pilot plants and industrial environments.
Energy-efficient heating technologies
Increasing the energy and resource efficiency of thermal processes is one of the department’s most fundamental task. In industrial combustion, special combustion processes such as direct flame impingement (DFI) and combustion with pure oxygen (oxyfuel combustion) can be used to increase the efficiency of existing processes. Preserving the integrity of the overall process is always prioritized with any project executed in this area.
Radiant tube technology
Indirect heating of industrial furnaces with radiant tubes is widely used in downstream processing of semi-finished products. The main work focus in this area lies on increasing the service life of metallic radiant tubes, which are subject to high creep deformation due to thermally induced stresses and changes in the thermal load. Furthermore, new radiant tube designs and concepts are currently being developed, tested and optimized for low pollutant emissions.
Several test rigs are available in our laboratory to investigate various radiant tube designs in short- and long-term tests. The investigations are complemented by coupled numerical simulation models, to calculate material stresses and deformations over the entire radiant tube life time. This is done by combining models for heat transfer and structural mechanics. Existing calculation approaches are continuously being developed and optimized.
Research projects
Ongoing research projects
- FlexLadleHeat — Flexible use of hydrogen and ammonia in ladle furnaces in the steel industry to reduce CO2 emissions (BMWK)
- BUTTERFLY – Biomass Utilized To The Extended portfolio of Renewable Fuels with Large Yields (Horizon Europe)
- TWINGHY — Digital twins for green hydrogen transition in steel industry (EU RFCS Big Ticket)
- HyInHeat — Hydrogen technologies for decarbonization of industrial heating processes (Horizon Europe)
- HydroConnect — Development of a software assistance system based on machine learning algorithms for decision making in heat treatment for use in SME industry to support the energy transition (progres.nrw Research)
- FlexHeat2Anneal — Flexible use of hydrogen as fuel in continuous annealing lines and hot-dip galvanizing lines in the steel industry to reduce CO2 emissions (BMWK)
- ZeroCO2Glas — Development of a novel hydrogen-fired glass melting furnace with the aim of a CO2-neutral container glass production (BMWK)
- CONDRA — Combined CO2 capture and energy saving at industrial furnaces by using decentrally generated pure oxygen (BMWK)
- Investigation on the influence of flexible operation modes of industrial furnaces on the lifetime of metallic high temperature components (AiF IGF)
Completed research projects
-
H2GlassTemp – Entwicklung eines modularen, wasserstoffbeheizten Temperofens für Glasbauteile (AiF ZIM)
-
H2MultiFuel – Entwicklung eines schadstoffarmen Verbrennungskonzepts für Wasserstoff zur Integration in Mehrstoffbrennersysteme (AiF ZIM)
-
BaSys4Brenner – Entwicklung einer zertifizierbaren und Industrie 4.0 tauglichen innovativen Brennersteuerung auf Grundlage der BaSys-Konzepte (BMBF)
-
Effizienzverbesserung des Kupolofens durch in-line Sauerstofferzeugung (AiF IGF)
-
FLOX‑2 – Mehrstufige flammlose Oxidation als Beitrag zur CO2-neutralen Prozesswärmeerzeugung (BMWK)
-
ReOrgAl – Steigerung der Energie- und Ressourceneffizienz des Recyclings organik-kontaminierter Al-Schrotte – ReOrgAl (BMWK)
- H2RadiantTube — Hydrogen from renewable energies as fuel in the radiant tube (progres.NRW Research)
- Development of a novel, flexible machining process for the production of quartz glass components (AiF ZIM)
- Tailored Heating in Hot Forming (AiF IGF)
- Development of innovative regeneratively heated radiant tubes for use in heat treatment furnaces with small installation space (AiF ZIM)
- Development of a recuperator for hybrid combustion air preheating in industrial furnaces (AiF ZIM)
- Influence of thermal load changes on the service life of highly loaded furnace components made of metallic high-temperature materials (AiF IGF)
- Development of an energy-efficient burner for heat treatment plants with a low-oxidising protective gas atmosphere (AiF ZIM)
- Extension of the application limits of FLOX technology for small and large burner capacities (BMWi)
- Increase of lifetime of metallic recirculating radiant tubes for industrial furnaces by reduction of thermal stresses (AiF IGF)
- Process development for low-scale reheating of semi-finished metal products (AiF IGF)
- Increasing the service life of metallic components in industrial furnace construction (AiF IGF)