FlexHeat2Anneal: Flexible use of hydrogen in continuous annealing lines and hot-dip coating lines to reduce CO2 emissions in the steel industry
Funding by the BMWK as part of the Federal Government’s 7th Energy Research Programme – Call for Proposals “Hydrogen Technology Offensive”, 1 April 2022 to 31 March 2025 (3 years)
Project description
The FlexHeat2Anneal project is being carried out by the Institute for Industrial Furnaces and Heat Engineering (IOB), together with WS Wärmeprozesstechnik GmbH and thyssenkrupp Rasselstein GmbH, to investigate the flexible use of hydrogen as a fuel in continuous annealing lines and hot-dip coating plants.
The background of the project is the European goal to become climate-neutral by 2050, which has resulted in the need for the steel industry to find alternative energy sources to massively reduce the CO2-emissions from heat treatment plants. Hydrogen produced from renewable energies, so-called green hydrogen, represents a promising alternative to the previously used fossil natural gas, as it burns locally without CO2-emissions. Thyssenkrupp Steel Europe GmbH and thyssenkrupp Rasselstein GmbH alone operate ten fire coating plants and four continuous annealing lines with an annual production capacity of 5.5 million tonnes of steel. The complete conversion of these plants to hydrogen would result in a reduction of 420,000 tonnes of CO2 per year.
The production of steel strip requires an additional annealing step after cold rolling. This process is used to adjust the mechanical properties and restore the formability of the strip. The strip is recrystallized at temperatures between 670 °C and 900 °C and the heat treatment can be carried out in both bell annealing furnaces and continuous annealing lines. In the latter, the strip passes through the furnace under a defined protective gas atmosphere (usually a mixture of 95% N2 and 5% H2). This protective gas atmosphere prevents oxidation of the strip surface during heat treatment. The heating of continuous annealing furnaces is usually done with self-recuperative burners that use preheated air to combust fuel gases. However, due to the defined atmosphere in the furnace, the separation between combustion gases and protective gas atmosphere must be ensured using radiant heating tubes. To ensure even heating of the strip in vertical plants, several radiant tubes, each with a burner, are installed. However, burner and radiant tube systems have so far been optimized primarily for applications with natural gas or blast furnace gases.
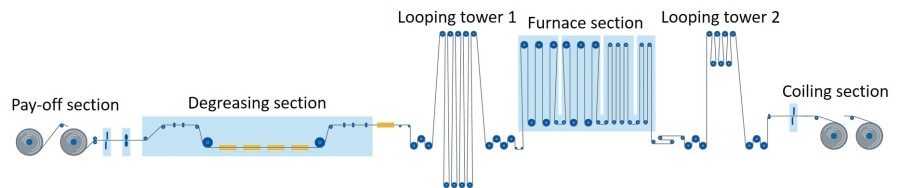
Fig.1: Schematic view of a continuous annealing line for tinplate [Source: thyssenkrupp Rasselstein GmbH]
When integrating hydrogen into existing systems, it is important to keep flexibility in mind and give the operator the ability to respond to price or availability fluctuations in the coming years. Therefore, the development of a fuel-flexible burner-radiant tube system is aimed at. The addition of hydrogen to fossil natural gas should be possible from 0 to 100 percent by volume without requiring manual adjustments to the system. Such a system offers a practical solution for the short- and long-term operation of low-emission plants.
To enable a switch to hydrogen, existing systems (PP and W heating tubes) will first be examined for the use of hydrogen and natural gas-hydrogen blends within the framework of FlexHeat2Anneal. Subsequently, a fuel-flexible and energy-efficient burner-radiant tube system will be developed together with WS Wärmeprozesstechnik GmbH. The new radiant tube systems will then be used and tested on an industrial continuous annealing line of thyssenkrupp Rasselstein GmbH for steel strip using two demonstrators.
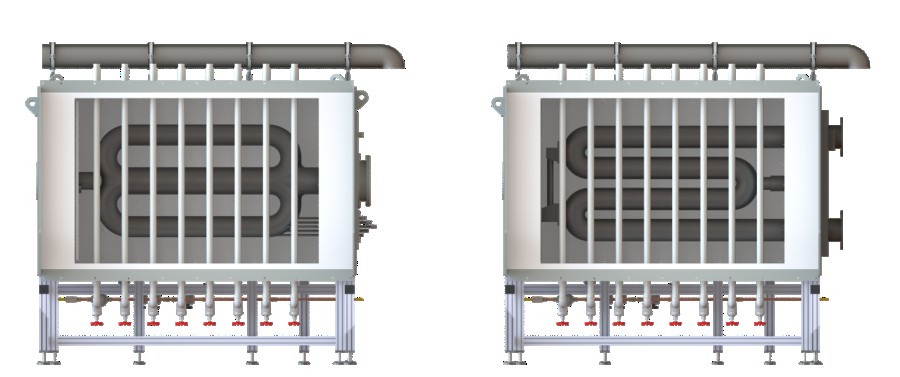
Fig.2: Modular test rig for the investigation of different radiant tube geometries (left: PP-type radiant tube, right: W‑type radiant tube).
The challenges in optimizing the system for natural gas-hydrogen mixtures lie in the different combustion properties of natural gas, hydrogen, and natural gas-hydrogen mixtures. The varying fuel composition makes it difficult to ensure high energy efficiency and constant power output, as well as to guarantee low NOx emissions. Accordingly, approaches to reduce NOx emissions, such as fuel staging or the FLOX® technology, are being tested and optimized for hydrogen and natural gas-hydrogen mixtures.
In addition to optimising and replacing the systems, the gas supply at the plant must also be adapted. Furthermore, the radiant tubes and burners must be equipped with measurement equipment to evaluate furnace operation, energy efficiency and pollutant emissions. Based on the results, the effects of switching from fossil natural gas to hydrogen for continuous annealing lines and hot-dip galvanising lines will be investigated and the true CO2 reduction potential will be determined.
Project goals
Flexible use of H2 as fuel in radiant tubes of annealing lines for steel strip
- Investigation of the use of hydrogen in existing radiant tube systems
- Development and demonstration of innovative, fuel-flexible and energy-efficient FLOX® radiant tube systems with lowest NOx emissions
Project participants
Further Information
Interview by Elsa Busson (IOB) and Dr Peter Kirchesch (ThyssenKrupp Rasselstein) for Industry Energy Research: “Fuel-Flexible Heating in the Steel Industry — We Want to Respond to Available Hydrogen Quantities at Short Notice”.
Contact
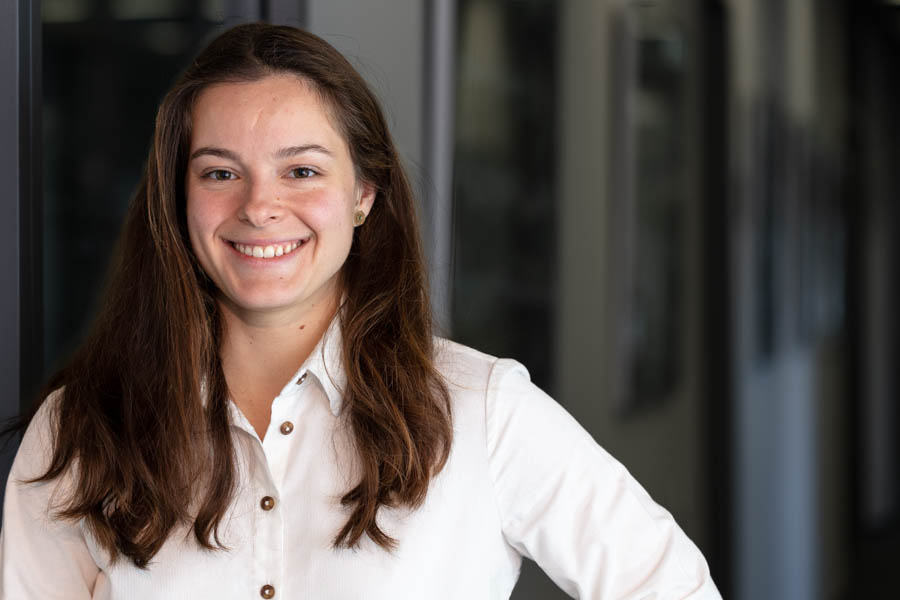
Fundings
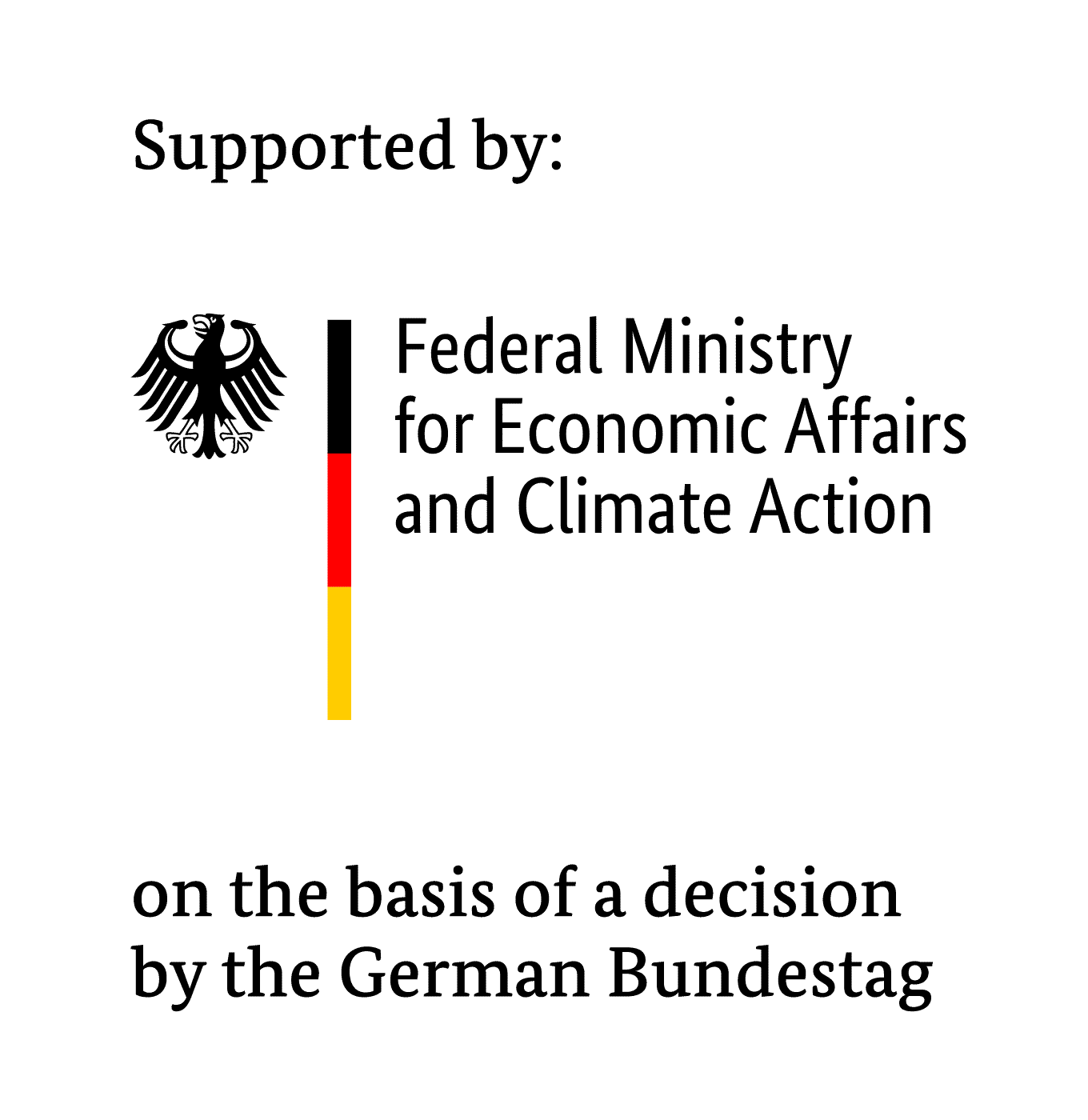
This project is funded by the German Federal Ministry for Economic Affairs and Climate Action (BMWK) under the funding code 03EN2078C.
Funding is provided within the framework of the 7th Energy Research Programme of the Federal Government.