FlexLadleHeat: Flexible use of hydrogen and ammonia in ladle furnaces in the steel industry to reduce CO2 emissions
Federal Ministry for Economic Affairs and Climate Action (BMWK) , 1 June 2024 to 31 Mai 2027
Project description
Ladles are used in the electric steel route to transport molten steel between the electric arc furnace, the secondary metallurgy and the casting plant. The ladles, consisting of a crucible-shaped steel structure, are lined with refractory materials for thermal insulation. The refractory is subject to continuous thermal stress during operation and is worn away and worn out in the process. For this reason, the refractory is regularly relined. After relining, the refractory material must be dried and preheated before being used with molten steel. This drying and preheating process takes place in the ladle management system.
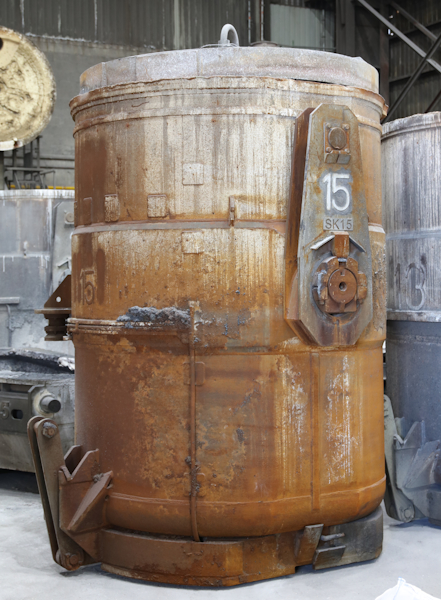
Transport ladle
In the ladle management system, horizontal ladle fires are used for preheating. Vertical ladle fires, in which the transport ladles stand upright, are used to dry the newly lined refractory. In the horizontal ladle fires, the ladle is preheated, and smaller jobs are carried out horizontally. During preheating, the ladle is closed with a lid in which the gas burner is integrated. The burners operate in the power range from 1 to 5 MW and are usually operated with natural gas-air mixtures. Oxyfuel systems with oxygen as an oxidiser are used to achieve higher efficiencies and lower exhaust gas losses. The transport ladles are preheated to over 1000 °C. Preheating the ladle reduces the heat losses of the melt in the ladle, lowers the necessary overheating in the electric arc furnace and thus reduces the tap-to-tap time. Ladle preheating is an indispensable part of steel production and the switch to heating with hydrogen-based fuels is therefore an important step towards CO2-neutral steel production.
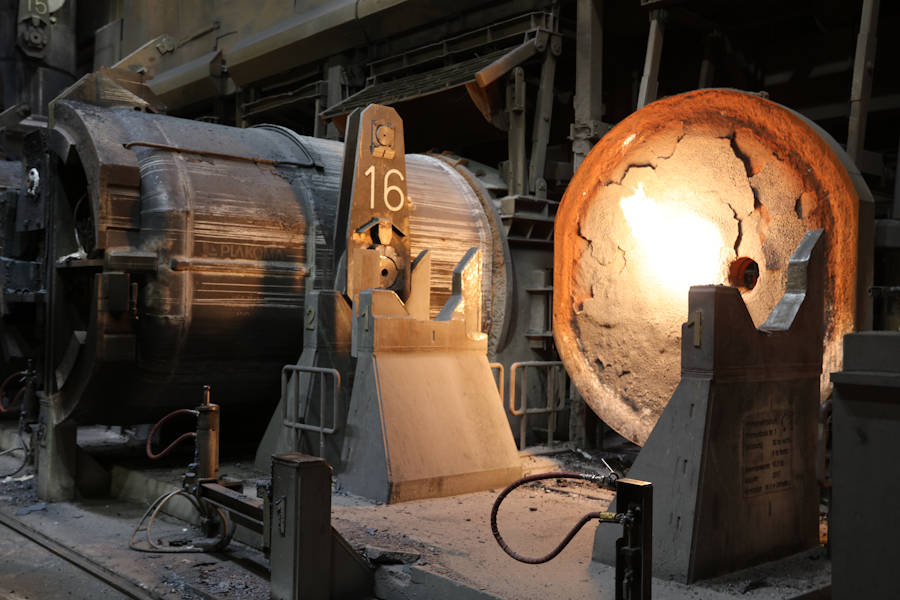
Ladle fire in open environment
In the FlexLadleHeat joint project, the Department for Industrial Furnaces and Heat Engineering (IOB) is developing an innovative ladle firing system for the flexible use of hydrogen and ammonia to preheat transport ladles in an electric steelwork together with the Chair of Ceramics at the Institute of Mineral Engineering (GHI), Badische Stahlwerke GmbH (BSW) and Badische Stahl-Engineering GmbH (BSE).
The project offers the potential to drastically reduce the CO2 emissions of Badische Stahlwerke’s ladle furnace system through the flexible use of hydrogen-based fuels. Hydrogen and ammonia are to be used in flexible proportions between 0 and 100 vol.-%, depending on availability. This includes the development of a new burner and safety technology, as well as control and regulation technology. By implementing a digital process model for ladle preheating, additional primary energy savings of up to 10 % are to be achieved in addition to the savings from oxyfuel operation.
The IOB’s task in this project is to develop digital process models based on numerical flow simulations (CFD) and to carry out experimental investigations of the ladle furnace system to validate the process models that have been developed. Numerical simulations are a proven tool in the design and optimisation of thermoprocessing systems and enable parameter studies to be carried out in a time and cost-efficient manner. As such, they can also be used to optimise ladle furnace systems and as a basis for the subsequent creation of a reduced furnace model that contributes to the efficient operation of the ladle furnace. The scope of suitable simulation models ranges from modelling actual fluid flow to models for turbulence, heat transfer by convection, thermal radiation and chemical (combustion) reactions.
Project goals
Development of an efficient oxyfuel combustion system for the use of hydrogen and ammonia for the preheating of transport ladles in the steel industry:
- Development of a fuel-flexible ladle firing system
- Optimization of ladle furnace operation with flexible fuel composition at a test plant in a steel mill environment
- Development of an innovative process model based on numerical simulations
- Material analysis of the refractory material on the influence of changing atmospheres and temperature curves during the preheating process
Project participants
Contact
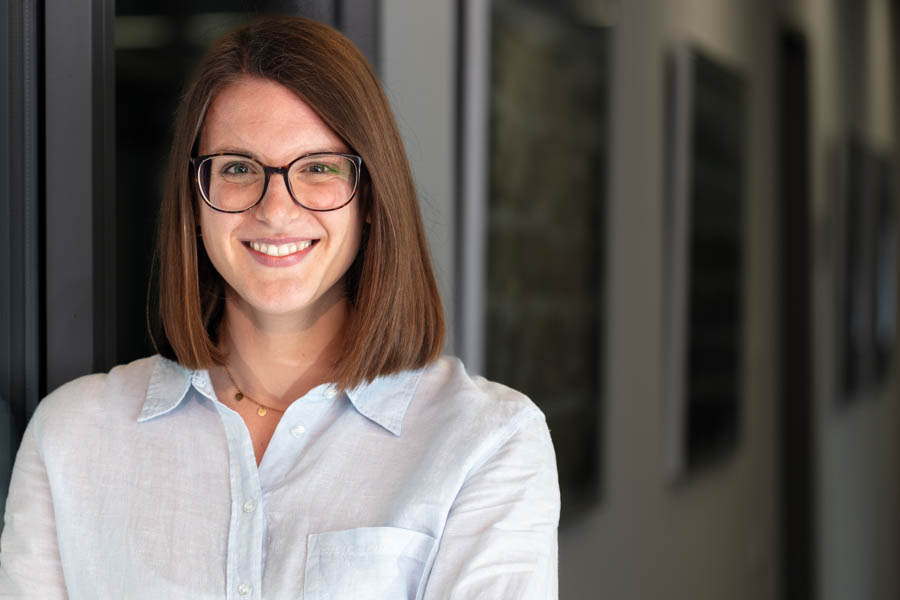
Funding
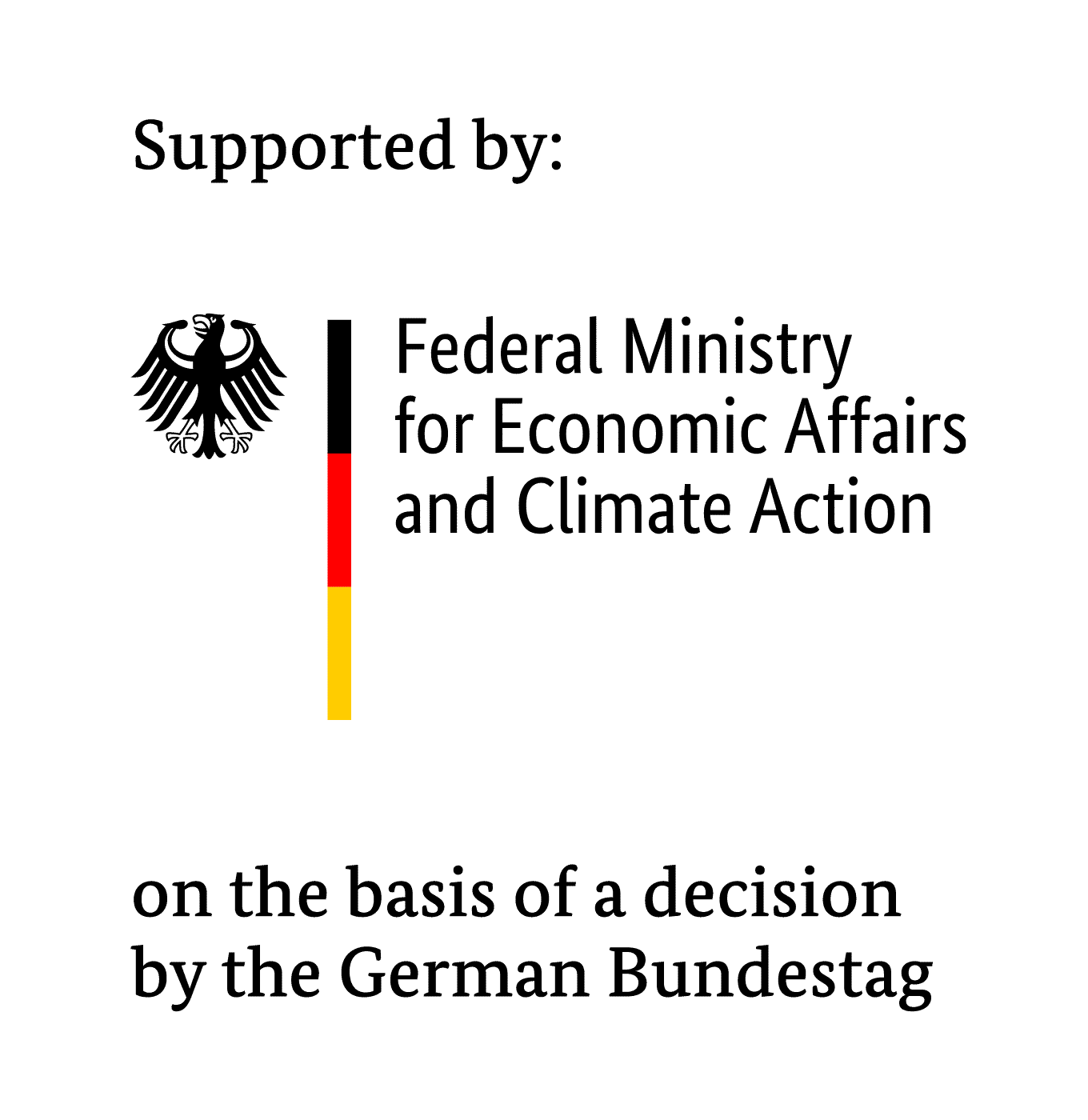
This project is funded by the German Federal Ministry for Economic Affairs and Climate Action (BMWK) under the funding code 03EN2117A.
Funding is provided within the framework of the 7th Energy Research Programme of the Federal Government.