Industrial Furnace Technology
Contact person: Dr.-Ing. Dominik Büschgens
Fields of activities
Heat transfer, fluid dynamics, process modelling, heat treatment, structural mechanics
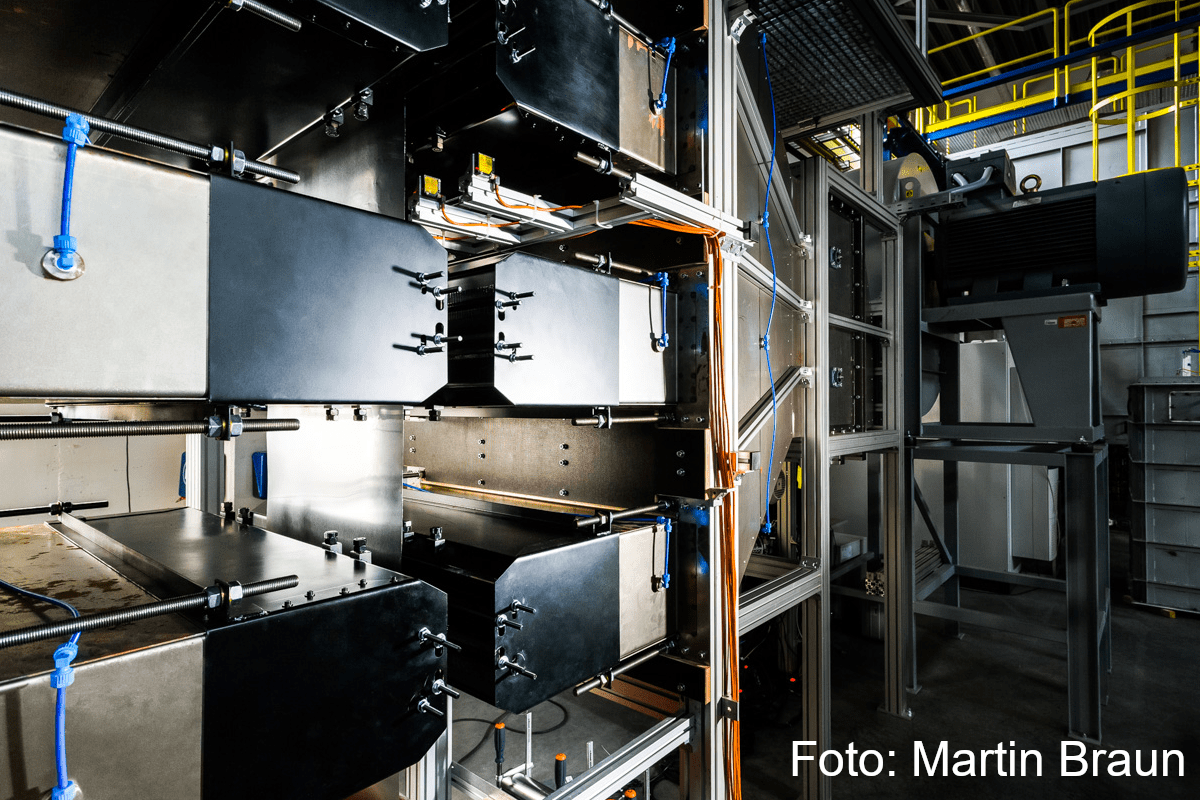
Areas of Research
To increase energy and resource efficiency in thermoprocessing plants, it is essential to have a thorough understanding of the heat transfer and fluid dynamics involved. For this purpose, the processes are modelled and subsequently investigated and optimized.
The research group operates a large number of test rigs, which are equipped with extensive and modern measurement technology. Furthermore, the experimental methods are complemented by analytical, (semi-)empirical models and numerical simulations (CFD/ FEM). A combination of experimental, analytical and numerical investigations enables a comprehensive representation of the physical processes.
Heat transfer in thermoprocessing plants
The heat transfer during heating or cooling of the material in an industrial furnace has a direct influence on the efficiency of the plant. Two main heat transfer mechanisms are involved — (forced) convection and thermal radiation.
The investigation on forced convection focuses on the flow of the fluid in thermoprocessing plants. In addition to the investigation of the macroscopic flow induced by fans, the local flow in the vicinity of the material is also highly relevant. It decisively determines the achievable heat transfer coefficients between the material and the fluid. These influence the heating and cooling rates that can be achieved in the process. Current research work is concerned with both gas and water quenching systems. The cooling rates that can be achieved under different aspects and problems that have a direct influence on the material properties are considered.
In the field of radiation-dominated processes, the research group is working on radiation models that allow the consideration of arbitrary two- and three-dimensional geometries. These are used for the development of process models, for example for flexible batch planning and prediction of the heating time of the material, in order to keep process times as short as possible and thus energy-efficient.
Fluid-structure interaction
Flow in industrial furnaces can lead to undesirable phenomena such as nozzle-induced strip vibration in annealing lines or horizontal strip flotation furnaces, which in turn can cause damage to the material or the furnace. Likewise, in combination with high temperatures, important plant components such as fans, can be damaged under certain operating conditions (e.g. due to eigen-oscillations at a given rotational speed). In addition to experimental investigations, the development of reliable numerical models of such phenomena is also a key focus.
Highly flexible heat treatment
The department’s own annealing simulator enables customized heat treatments to derive an optimum annealing cycle for metallic samples. For this purpose, any atmospheres (from inert gas up to 100 % hydrogen), as well as rapid heating and cooling rates can be set. The modular heat treatment facility also operated by the group allows, in addition to cooling with air, cooling with water under arbitrary nozzle fields, as well as selective tempering of samples with dimensions of max. 300 mm x 200 mm. With these test facilities, materials technology is linked to the process, which enables the detailed investigation of individual problems, but also the subsequent transfer to the industrial plant.
Structural integrity, lifetime optimization and prediction
In addition to the consideration of heat transfer and fluid dynamics in thermoprocessing plants, the thermally induced stress distribution of the plant components (e.g. radiant tubes, nozzle boxes) also plays a role in many applications. By applying numerical methods (e.g. FEM), thermal stresses can be calculated as a function of the temperature distribution and the restraint situation, and component failures can be predicted. A combination with creep models allows the extension of thermal stress models to lifetime prediction models.
Research projects
Ongoing research projects
- Defined setup of heat transfer profiles in spray nozzle fields for optimization of heat treatment in continuous strip plants (AiF IGF)
- CO2-neutral Saint-Gobain site Herzogenrath Feasibility studies — COSIMa (progres.NRW)
Completed research projects
- Development of a process model for a strip annealing line — HeatSteel (progres.NRW)
- Improvement of heat transfer in tube-bundle heat exchangers by using structured tubes (AiF ZIM)
- Decentralized Hydrogen Production from Biogas via Steam Reforming — BioH2Ref (BMWK)
- Development and experimental validation of numerical heat transfer models for impingement jets (AiF IGF)
- Process modelling of wire patenting in the lead bath and evaluation of lead-free alternatives (AiF IGF)
- Heat transfer at surface contacts in preheating and heat treatment processes (AiF IGF)
- Semantic interoperability of heterogeneous process models integrating process data to improve quality and save energy in coupled forming and thermal processes in the metal industry (AiF IGF)
- Increasing the thermomechanical stability of cross-flow fans for use in thermoprocessing plants (AiF IGF)
- New tunnel kiln concept for the saving of fossil energy and CO2 in the firing of bricks (AiF IGF)
- Impact of hydrogen on processes and materials during heat treatment
(AiF IGF) - Development of high-performance metallic heat exchangers for the expansion into new fields of application (AiF ZIM)
- Thermal characterisation of surface contacts (AIF IGF)
- Surface enlargement and lifetime increase of radiant tubes by the use of structured sheets (AiF IGF)
- New tunnel kiln concept for energy-efficient firing of bricks (AiF IGF)
- Development of an interactive batch planning system for plasma nitriding (AiF ZIM)
- Development of an innovative hot isostatic press for combined compression and heat treatment of semi-finished products and components (AiF ZIM)
- Influence of heat transfer on the process stability of continuous annealing lines (AiF IGF)
- Development of cross-flow fans for use in thermoprocessing plants (AiF IGF)
- Measuring large volume flows at high operating temperatures in industrial furnaces (AiF IGF)
- Investigations on the stability of metallic strips under the influence of nozzle fields (AiF IGF)
- Development of a multi-layer chamber furnace for press hardening of sheet metal for the automotive industry with the goal of improving economic efficiency (AiF ZIM)
- Volume flow measurement during high convection heat treatment (AiF IGF)