Development of energy efficient burners for heat treatment plants with reducing / protective gas atmosphere
The majority of the plants for heating semi-finished metal products, especially in the steel and copper industry, are operated with open natural gas heating. Combustion is generally overstoichiometric, so that considerable metal loss due to scaling and associated problems in process control and further processing are accepted. Increasing demands on the product and the process control lead to an increasing necessity for plant manufacturers and operators to avoid or reduce scale formation. In the field of heat treatment of semi-finished metal products, the use of protective gas for inert or reducing atmospheres is widespread. In many cases the protective gas is generated in external plants as exo- or endogas, which results in a cost-intensive integration into the existing infrastructure due to the increased number of required plant components.
The aim of the research project is the development of a novel, innovative burner based on a recuperative burner with integrated process gas afterburning in a flame tube to improve the efficiency of plants for the heat treatment of metallic components in a reducing inert gas atmosphere. This innovative product is realized by the use of gas-heated recuperative burners, which generate an inert oxidation atmosphere directly in the furnace through the sub-stoichiometric combustion of natural gas and air, as an alternative to the generation of the atmosphere with exogas plants. The complete burnout of the still combustible furnace atmosphere takes place before the heat exchanger in a flame tube of the burner and is used directly via radiation in the furnace. The joint research project comprises the experimental and numerical design, construction and manufacture of a prototype of the burner.
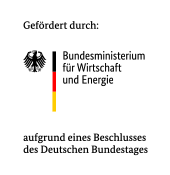
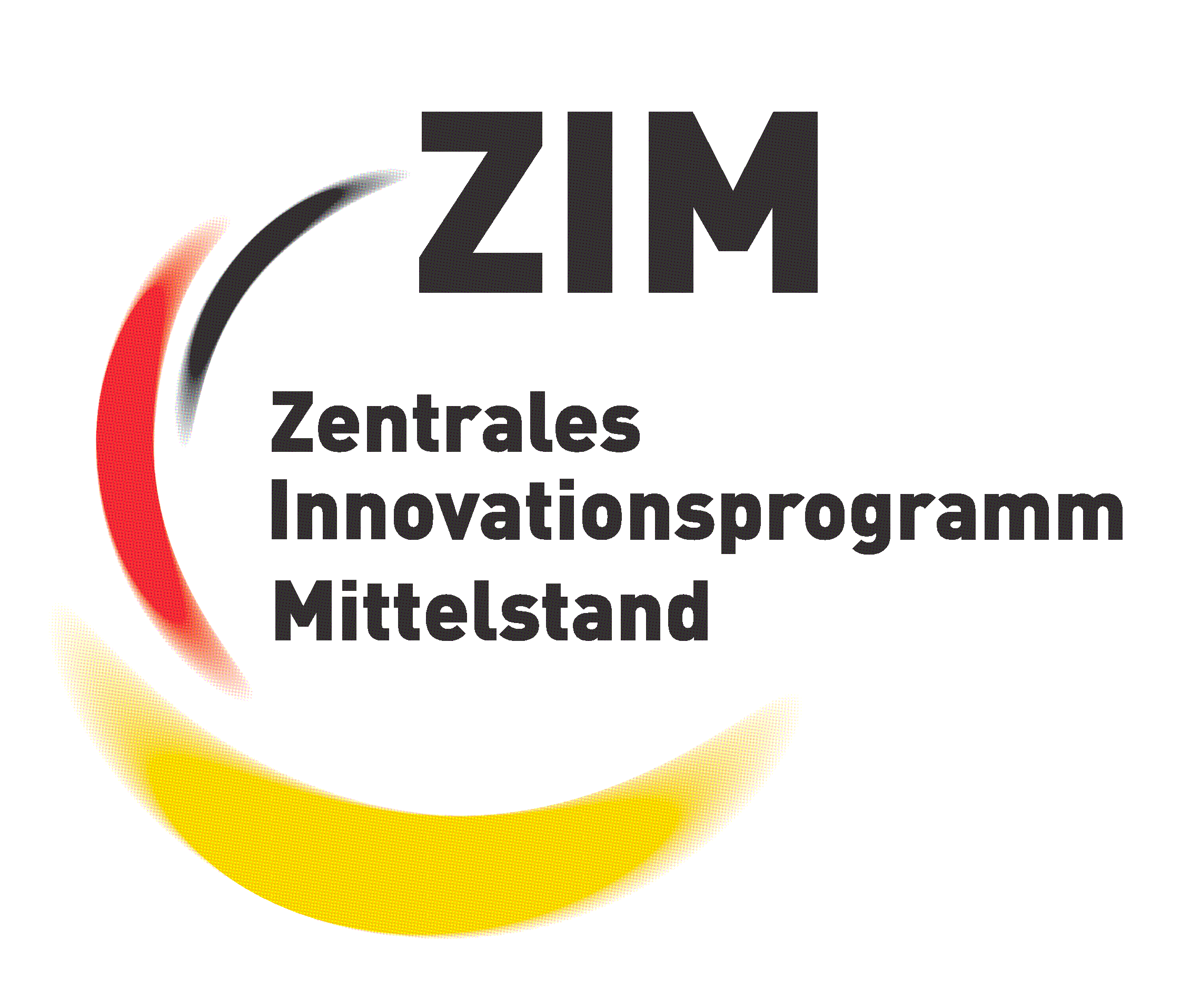
The research project with the funding code ZF4042201ST5 was funded by the Federal Ministry of Economics and Energy on the basis of a resolution of the German Bundestag.