Improvement of the service life of metallic components in industrial furnace engineering
Depending on the application, industrial furnace plants are exposed to different thermal loads (heat treatment: aluminium T~550°C, steel T~850°C). However, it is not the average application temperature of the furnace that poses a problem for the durability of the furnace construction or furnace components, but local temperature peaks and temperature gradients, as these generate thermally induced stresses. The aim of the project is to increase the service life of highly stressed furnace components (e.g. radiant heating pipes, muffles) already in the design phase by means of improved simulation techniques. This gives the SME the direct possibility to optimize the failure of the investigated components and thus the economic efficiency of the built plants. The main benefit is that optimized components have optimized material usage and minimized failure probabilities, which enables the plant constructor to either offer his plants more cost-effectively or to increase profits. The reduced frequency of failures also reduces recourse claims. This is to be achieved by a holistic process simulation. This leads to a coupling of the flow and thermal conditions in the furnace (CFD-Computational-Fluid-Dynamics) with the temperature and stress distribution (CSD-Computational-Structure-Dynamics) in the component under consideration. This so-called fluid-structure interaction (FSI) is a new approach for the description of coupled problems. After coordination with the PA, the numerical and experimental investigations of a metallic P‑radiant heating tube are proposed. Experimental investigations serve primarily to validate the simulation. The numerical investigations, on the other hand, should provide a deeper understanding of the physical processes taking place.
The aim of the research project was to increase the service life of metallic furnace components in industrial furnace construction by taking a holistic view of the processes involved with their thermal and mechanical parameters. This led to a coupling of the flow and thermal conditions in the furnace with the temperature and stress distribution in the component under consideration. Finally, it can be stated that the coupled consideration of flow and thermal conditions with the stress distribution enables a significantly more exact prognosis of the occurring stresses compared to the classical calculations on the basis of homogeneous temperature distribution or heat flux density. This enables the plant constructor to identify critical areas already in the design phase and to take appropriate measures.
Final report
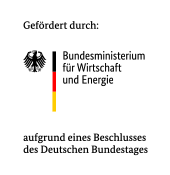
This research project was applied for by the Forschungsgemeinschaft Industrieofenbau e.V. via the Forschungskuratorium Maschinenbau e.V. and financially supported by the Bundesministerium für Wirtschaft via the Arbeitsgemeinschaft industrieller Forschungsvereinigungen e.V., AiF-Nr. 15698 N.