Improvement of product quality and economy of industrial furnaces with protective gas atmosphere by optimization of the change of furnace atmosphere
The importance of annealing processes under inert gas or reaction gas has been increasing for years. In particular, the requirements for the quality of process gas atmospheres, especially for highly flammable or flammable process gases, are generally very high due to the required personal and plant safety.
The flushing of the free furnace volume with non-combustible gases to carry out a safe atmosphere change can be carried out under all process conditions. The free furnace volume is purged with purge or process gas until the concentration of the process-relevant gas components reaches the target values with regard to safety and quality.
The research objective is a deeper knowledge of the atmosphere change in discontinuously operated inert gas furnaces. The aim is to analyse the efficiency of different gas exchange strategies. This will make it possible to identify influencing parameters and incorporate them into new concepts for atmosphere change.
The target size is to reduce the required specific gas quantity and the purging time (increase productivity). The parameters investigated are:
- Arrangement and design of gas inlets and outlets,
- purge gas volume flow,
- Process gas volume flow (volume flow circulated by fan).
For this purpose physical and numerical simulations on cold models as well as investigations on an industrial protective gas chamber furnace have been performed.
The results of the laboratory tests without fan (forced circulation) show that
- inlet and outlet diameters have a very small influence on the atmospheric change with the same spatial arrangement.
- a spatial variation of the inlets and outlets has a considerable influence on the forming flow structures but due to the high turbulent mixing has only a small influence on the entire gas exchange, so that the course of the atmospheric change in all variants has almost equalized up to θ = 5.
Laboratory tests with fans have shown that
- with the gas circulator running, free convection, caused by temperature or concentration gradients, plays a negligible role in atmospheric change.
- the arrangement of the purge gas inlets only plays a role at the beginning of the gas change; in the further course of the study, all the variants examined converge.
- the circulated volume flow (gas circulator) and the purge gas volume flow also only have an influence at the beginning of the atmosphere change.
The operating tests on the inert gas chamber furnace show that
- the atmosphere change under operating conditions (hot test) reaches the O2 safety limit of 1 % within the 5‑fold safety flushing quantity θ = 5; this is not safely achieved in the cold test.
- a higher furnace temperature significantly accelerates the atmosphere change.
For security reasons it must be noted that
- just in the case of furnaces that had been out of operation for longer periods, it must be noted that the furnace design and insulation can delay the first atmosphere change due to poor flow (dead space areas).
- the monitoring of 5 times the amount of safety purge gas (DIN-EN 746–3) is not sufficient as a safety criterion for the atmosphere change. The additional monitoring of safety-relevant gas components is necessary at critical locations.
Final report
Bölling, R.; Valente-Simoes, J.-P.; Pfeifer, H.: Verbesserung von Produktqualität und Wirtschaftlichkeit von Industrieöfen mit Schutzgasatmosphäre durch die Optimierung des Atmosphärenwechsels, FOGI-Nr. FV 679, Forschungsgemeinschaft Industrieofenbau e.V., Frankfurt
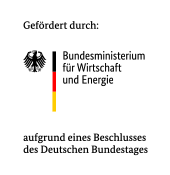
This research project was applied for by the Forschungsgemeinschaft Industrieofenbau e.V. via the Forschungskuratorium Maschinenbau e.V. and financially supported by the Bundesministerium für Wirtschaft via the Arbeitsgemeinschaft industrieller Forschungsvereinigungen e.V., AiF-Nr. 14153 N.