Experimental and numerical investigations of the multiphase flow in the water model of a steel casting ladle as a basis for further development of the multiphase models in the flow simulation of metallurgical reactors
DFG Project RU 2050/2–1
Increasing industrial demands for high-performance steels with the highest degree of purity and homogeneous, optimum technological properties for life-enhancing components require a comprehensive understanding of the processes involved in secondary metallurgy. This provides opportunities to improve plant productivity and product properties.
A detailed knowledge of the multiphase flow in the water model of a ladle as a function of various parameters deepens the basic understanding of the process and its influencing variables. Furthermore, the data form the validation basis for the further development of numerical models for the simulation of the flow in the ladle. Experiences gained during the investigations at the AOD converter show that CFD models validated with water models in the field of multi-phase flow with heterogeneous buoyancy free steels are capable of reproducing the real process well after transfer to it. It could also be shown that for the water model observed influencing variables are qualitatively transferable to the real process.
The present research project aims at understanding the basic mechanisms of the formation of the heterogeneous buoyancy free jet as well as the resulting flow in the ladle and to apply this knowledge to the further development of numerical models which realistically describe the reactor in the field of multi-phase flow. Especially in the field of numerical description of multiphase flows in metallurgical reactors there is a need for comprehensive research. Especially numerical models validated with modern experimental methods are not very common in the literature.
Buoyancy-free jet in the water model of a continuous casting ladle
Within the framework of the research project, various influencing variables on the flow in the ladle will be investigated in detail experimentally. Furthermore, numerical models will be further developed, which are able to describe the complex process macroscopically. These models form the basis for further process improvements. By a correct simulation of the bubble size distribution as well as the velocity of the bubbles and the shape of the heterogeneous buoyancy free jet, models for the energy and mass transport in the investigated processes (e.g. modelling of the chemical reactions) can be developed, based on the flow simulations. On the basis of the models developed, the geometry of ladles and injection systems can be optimized in order to shorten the process time. In this way, energy and resources can be saved.
Publications within this project
Haas, T.; Rückert, A.; Pfeifer, H.: Numerical modelling of the bubble driven flow within a steel ladle validated by particle image velocimetry, 7th International Conference on Modelling and Simulation of Metallurgical Processes in Steelmaking (STEELSIM2017), 16.–18. August 2017, Qingdao, China
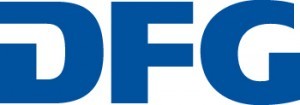