Sustainable aluminium recycling: Efficient melting
In the Advanced Metals And Processes Research Cluster (AMAP), various research units and companies work together on pre-competitive problems. The “Project 5 — Aluminium Recycling”, in which the IOB is involved, deals with the modelling of the heating and melting process of aluminium scrap (e.g. beverage cans, so-called UBCs — “used beverage cans”, see Figure 1). Compared to the production of primary aluminium, the recycling of used aluminium (such as beverage cans) is more energy-efficient and at the same time leads to significantly lower CO2 production.
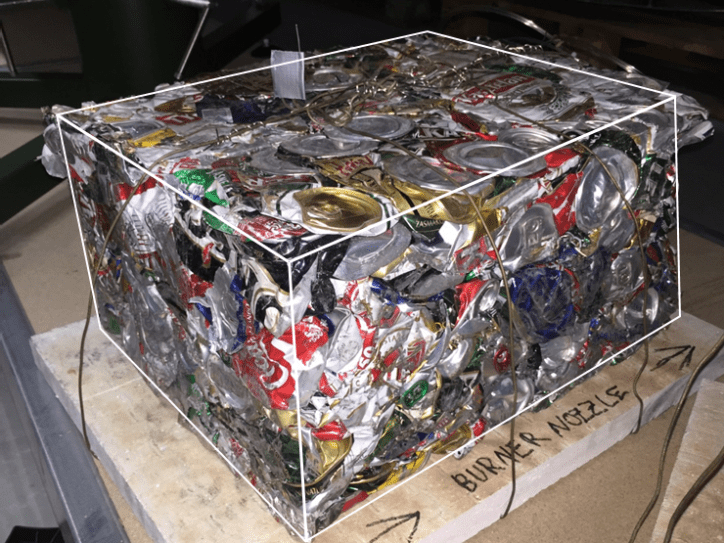
The melting down of aluminium scrap is an important process in the recycling chain and requires a detailed consideration of all the mechanisms involved. A better understanding of these mechanisms, e.g. heat transfer or pyrolysis, leads to a further optimisation of the recycling concept. Questions concerning metal losses and organic contamination of aluminium scrap will be investigated.
The main task of the IOB within the AMAP P5 consortium is to generate a CFD simulation of the different investigated phenomena. The contributions investigated at the IOB are the modelling of the combustion process, in particular the flameless combustion, the (radiation) heat transfer to the material to be melted as well as the pyrolysis of the adhering organic material (paints and cooling lubricants).
A characteristic feature of flameless combustion is the strong recirculation of the combustion products, which results in a reduced combustion temperature and a spatially extended reaction zone. The absence of temperature peaks and thus of a flame front causes a reaction zone that cannot be detected by the human eye. A numerical calculation of this process with the already implemented models is not possible and requires an extension of the chemical reaction mechanisms. Figure 2 shows the OH° concentration on the middle plane of a pilot furnace model. Compared to conventional combustion, this is not concentrated at the burner mouth, but protrudes relatively far into the furnace. The temperature peaks, at approx. 900 °C, are also well below the adiabatic combustion temperature and thus correspond to the flameless conditions.
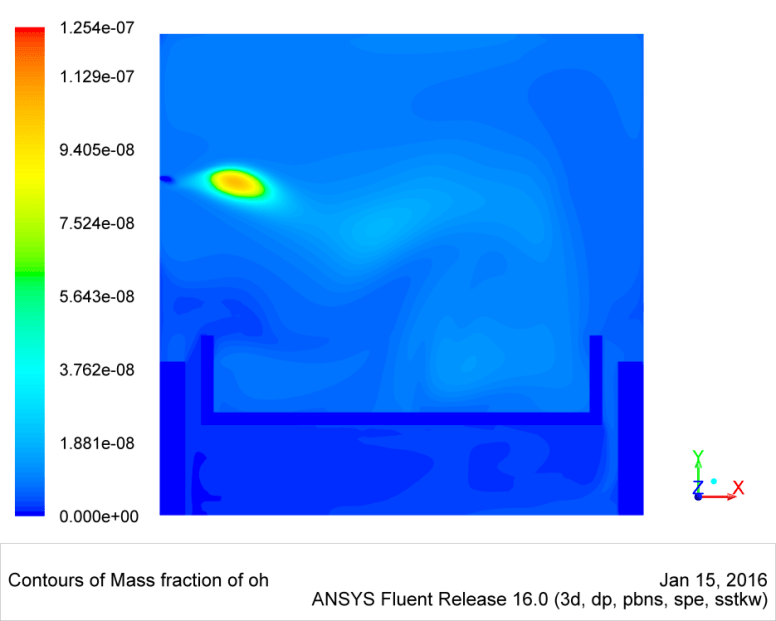
The furnace walls heated by the described combustion provide part of the heat transfer to the material in the form of radiant energy. In order to calculate the radiant heat transfer to a feed material modelled as a porous medium, the radiation models provided by commercial solvers must be further developed. This is also being worked on by the IOB.
Another part of the AMAP P5 is the investigation of the pyrolysis gas emissions already mentioned above from various organically contaminated scrap metals during heating. On the basis of experimental investigations the pyrolysis gas emissions are characterized in order to be able to observe the interactions of such gases with the melt and to integrate the emission into CFD simulations. For this purpose, small quantities of the material to be investigated are heated on a laboratory scale with a defined heating rate from room temperature to just below the melting point. At temperatures from approx. 350 °C decomposition reactions of the organic components take place which lead to tar, oil and gas emissions. Resulting gases are analyzed with analysis systems (FTIR etc.). The knowledge gained allows conclusions to be drawn about the decomposition processes and reaction mechanisms as well as about the caloric contribution of the gases to the furnace energy balance.