Energy and Mass Balances
Contact person: Dr.-Ing. Thomas Echterhof
Fields of activities
Energy and mass balancing, electric steelmaking process, process modelling, off-gas analysis
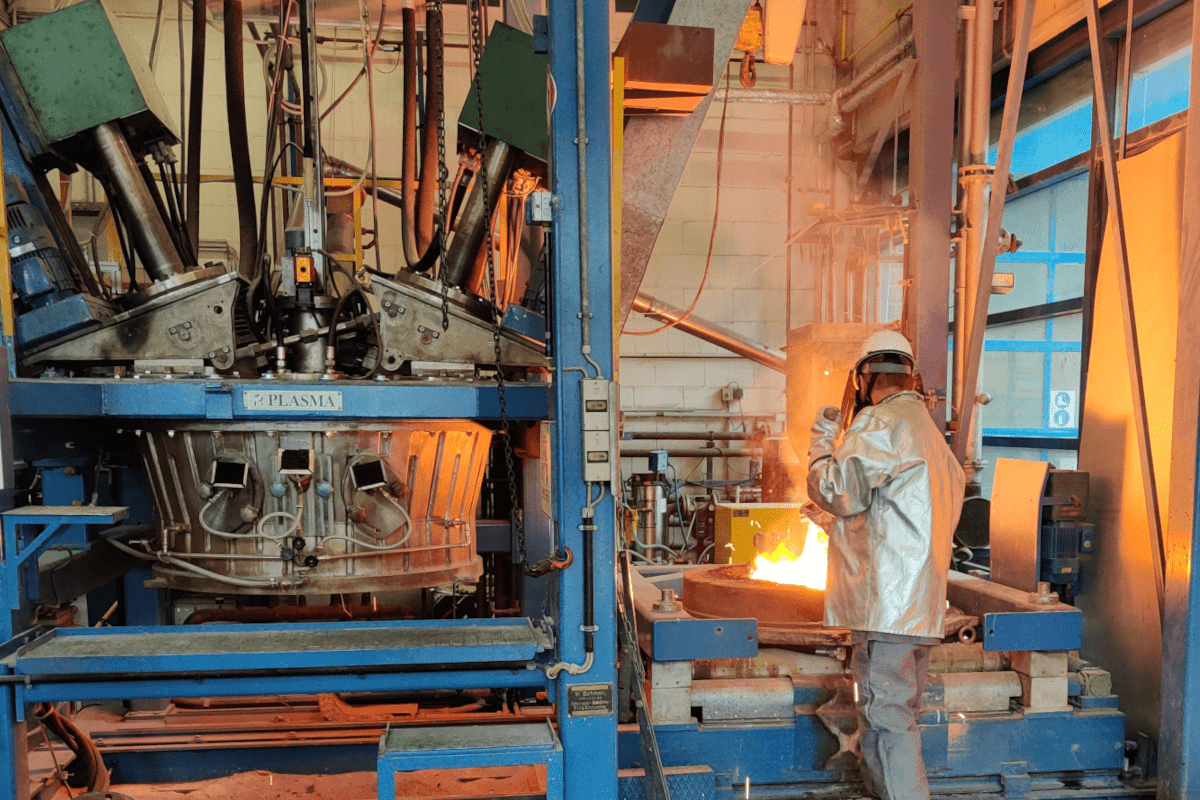
Areas of research
Energy and resource efficiency
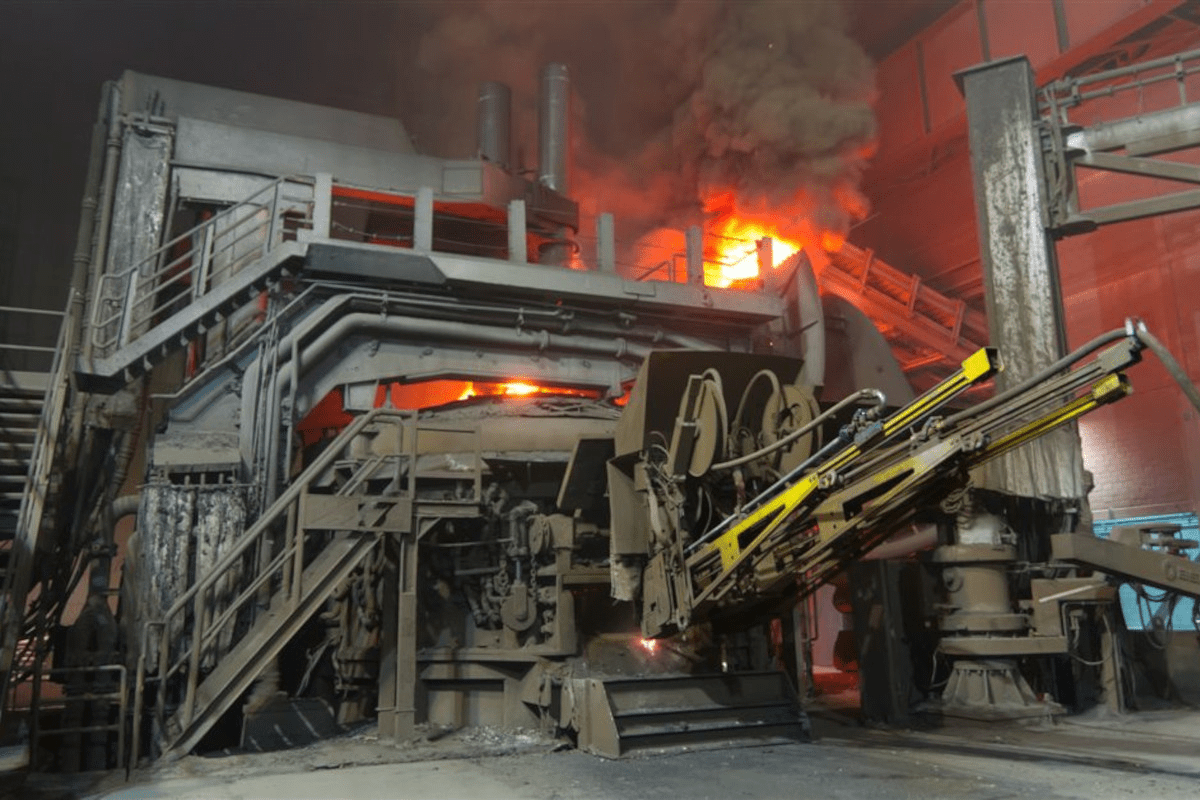
Increasing the energy and resource efficiency of steel production in the electric arc furnace has been a central topic for research and development in this working group for many years. Much of this work is based on the analysis of existing processes by drawing up energy and mass balances and the process optimisation derived from them.
For the preparation of balances and also for the development of process control strategies, the group draws on many years of experience in the installation and operation of off-gas analysis systems on industrial high-temperature units such as the electric arc furnace. In addition, the working group operates an electric arc furnace on a pilot plant scale at the Herzogenrath site.
The testing and implementation of new measurement technology at the electric arc furnace, but also the development of new agglomeration processes for residues and by-products of the electric steelmaking route, contribute to an increase in the energy and resource efficiency of the processes as well as cross-process circular economy approaches.
Decarbonisation and environmental technology
In the past, off-gas measurements on electric arc furnaces were used to determine environmentally relevant mass flows (NOx, CO2). In addition to determining the current status, basic principles of the formation and process strategies for reducing or avoiding environmentally relevant NOx emissions were developed and investigated both in the pilot plant and in industry.
A particularly important area is currently research into decarbonisation, i.e. the substitution of fossil carbon carriers with e.g. biomass and biocoal as well as hydrogen in the electric steelmaking process. Here, too, investigations have been and are being carried out both on a laboratory and pilot plant scale as well as in industry.
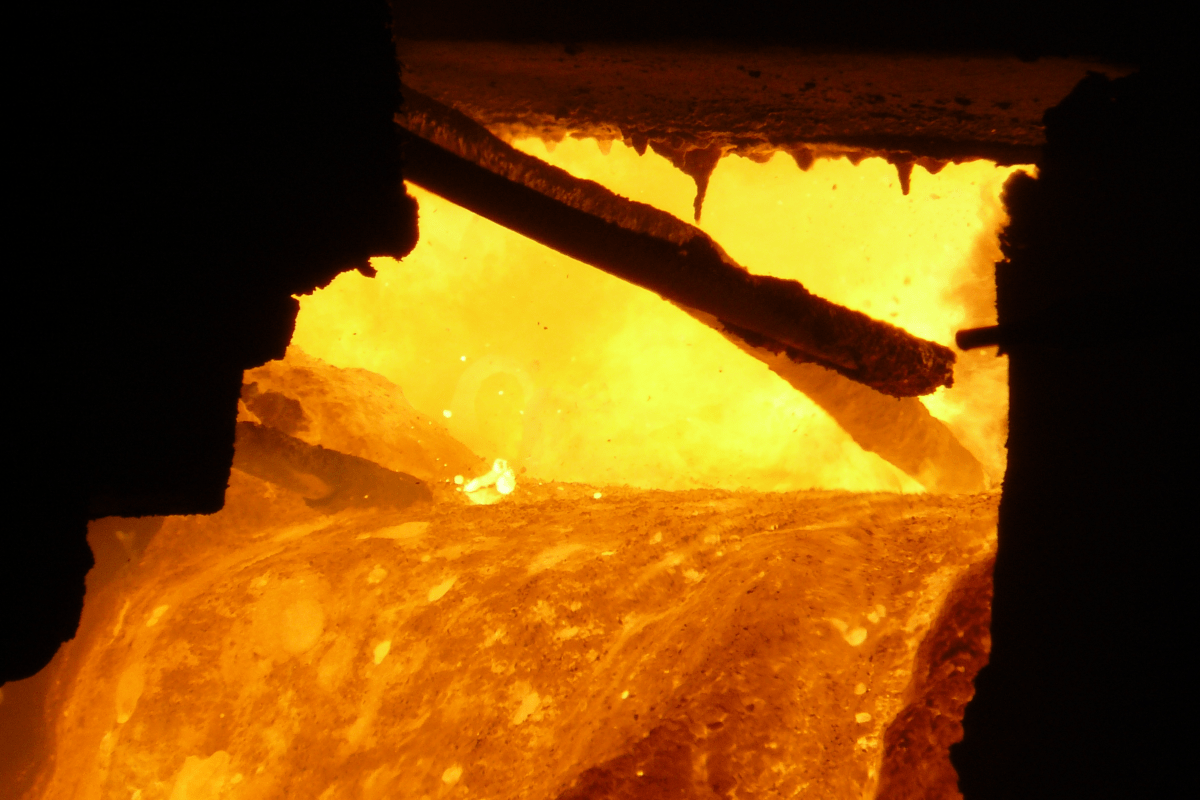
Process modelling
Process modelling is carried out on the basis of mathematical modelling and machine learning methods. A dynamic process model for simulating the processes in the electric arc furnace is available in the working group and is continuously further developed. In addition to academic research on and with the process model, it is also implemented in industry to support flexible and optimised process control. Furthermore, the process model of the electric arc furnace is also being made accessible for teaching and further education.
Research projects
Ongoing research projects
- Recovering valuable materials from metal-containing, dusty production residues through fibre waste-based briquetting — FaBrik (BMBF)
- Reduction of CO2 emissions through the flexible and efficient use of different energy sources at the electric arc furnace – FlexLBO (BMBF)
- Developing and enabling H2 burner utilization to produce liquid steel in EAF — DevH2forEAF (EU RFCS)
- Increasing the resource efficiency of metallurgical processes by agglomerating slags, dusts and sludges using stamp presses – ReMPA4S (AiF IGF)
Completed research projects
- Retrofitting equipment for efficient use of variable feedstock in metal making processes – REVaMP (Horizon 2020)
- Development of a novel, modular retrofit package for electric arc furnaces up to 20 t (AiF ZIM)
- Cement-free brick production technology for the use of primary and secondary raw material fines in EAF steelmaking – Fines2EAF (EU RFCS)
- Development of a reference model for the life cycle assessment of electric steelmaking for process optimisation and CO2 savings – EcoSteel (BMBF)
- On-line slag composition analysis for electric arc furnaces – OSCANEAF (EU RFCS)
- Biochar for a sustainable EAF steel production – GREENEAF2 (EU RFCS)
- Valorisation and dissemination of EAF technology – VALEAF (EU RFCS)
- Development of an agglomerate brick from ladle slag and biocoal for use in the electric arc furnace in steel production (AiF ZIM)
- MegaCarbon – Resource-efficient and highly productive production of carbon fibres for a wide range of applications (Ziel 2 NRW EFRE)
- Development of a modular, retrofittable and energy-efficient vessel technology for electric arc furnaces (AiF ZIM)
- Sustainable EAF steel production – GreenEAF (EU RFCS)
- Increasing energy and resource efficiency in electric steelmaking through holistic, quality-guided production control – ENRECO2 (BMWi)
- Control of Nitrogen Oxide Emission at the Electric Arc Furnace – CONOX (EU RFCS)
- Improved EAF process Control using On-line Offgas Analysis – OFFGAS (EU RFCS)
- Fundamental investigations on the formation of nitrogen oxides in the electric arc furnace (DFG)
- Development of operating conditions to improve chemical energy yield and performance of dedusting in airtight EAF (EU ECSC)