TWINGHY: Digital TWINs for Green HYdrogen transition in steel industry
Research Fund for Coal and Steel, 1 February 2023 to 31 July 2027
Project description
In the EU-funded research project TWINGHY — Digital TWINs for Green HYdrogen transition in steel industry — the decarbonization of the reheating process in the steel industry is demonstrated. To this end, two hybrid natural gas-hydrogen burners for combustion with air and oxyfuel are developed and installed in a reheating furnace together with the required infrastructure. An additional focus is on the digitalization of the process. In the course of the project, digital twins of two reheating furnaces will be developed. A data-driven approach and a physically based approach will be pursued and compared eventually. In order to feed the digital twins with data, the measurement technology of the furnaces will be expanded and supplemented by comprehensive CFD simulations.
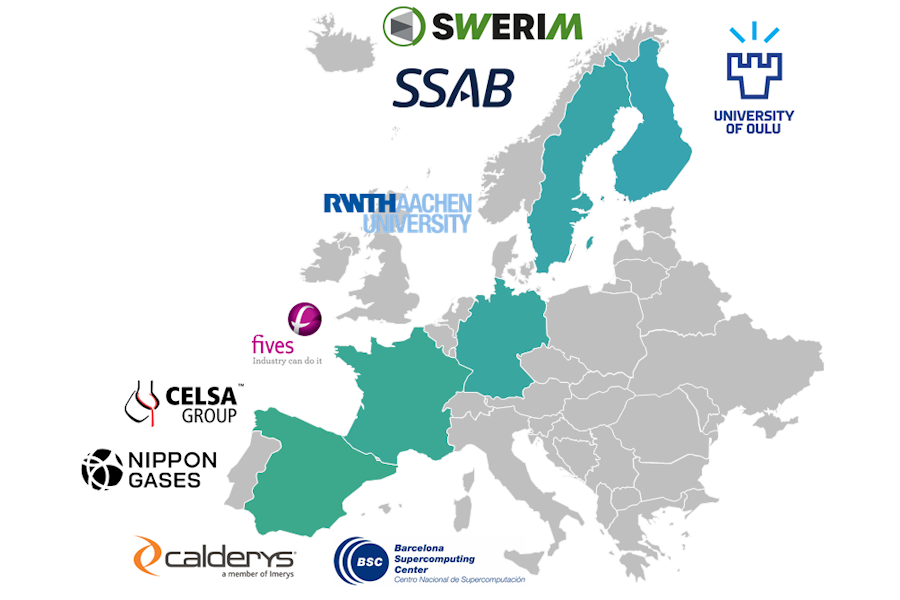
Consortium of the research project
The broad-based consortium is made up of partners from industry, research institutes and universities. The industrial-scale furnace demonstrators are provided by the steel producers Celsa Group and SSAB. The hybrid burner for combustion with air is developed by furnace manufacturer Fives. Gas supplier Nippon Gases is supplying a new burner for firing with pure oxygen and is building the necessary infrastructure for hydrogen and oxygen supply at the site. The corresponding activities are coordinated by project coordinator Celsa, in whose walking beam furnace the research work has to be reconciled with the day-to-day production cycle. IOB is carrying out measurement campaigns before and after the retrofit of Celsa’s furnace in order to quantify the effects on the process. The data obtained will be used to set up and validate efficient RANS-CFD simulations of individual burners and the entire furnace. The high-resolution benchmark for these simulations is provided by the Barcelona Supercomputing Center (BSC) in the form of large-eddy simulations. The data from regular operation and additional measurements also help the BSC to model the process using neural networks. The data-driven digital twin obtained in this way is compared with a finite element process model derived by Swerim from the physical laws governing heat transfer. In parallel to the developments, the influences of the fuel change on the refractory are analyzed by the Institute of Mineral Engineering at RWTH Aachen University (GHI) and the refractory manufacturer Calderys. In the course of this, laboratory trials are conducted with material samples exposed to the altered conditions with regard to the increased water content in the furnace chamber and locally changed temperatures. Samples are also introduced in the furnace to collect data on the real demonstrator. In addition to the refractory, the product also experiences the altered atmosphere in the furnace chamber. Corresponding tests are carried out at the University of Oulu to ensure that the change in fuel does not affect product quality.
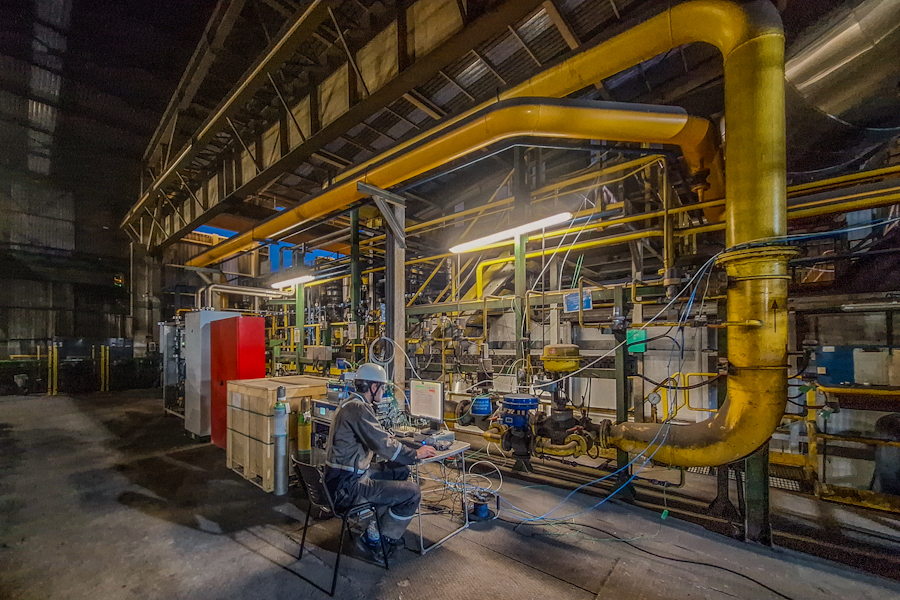
Measurement campain at the reheating furnace at the Celsa 3 steelworks
Project goals
- Retrofit of the heating zone of a walking beam reheating furnace to fuel-flexible natural gas/hydrogen burners
- Increase of process efficiency and decrease of NOX emissions by employment of oxyfuel
- Development of a digital twin for the reheating process
- Investigation of influences on refractory and product
Project participants
Contact
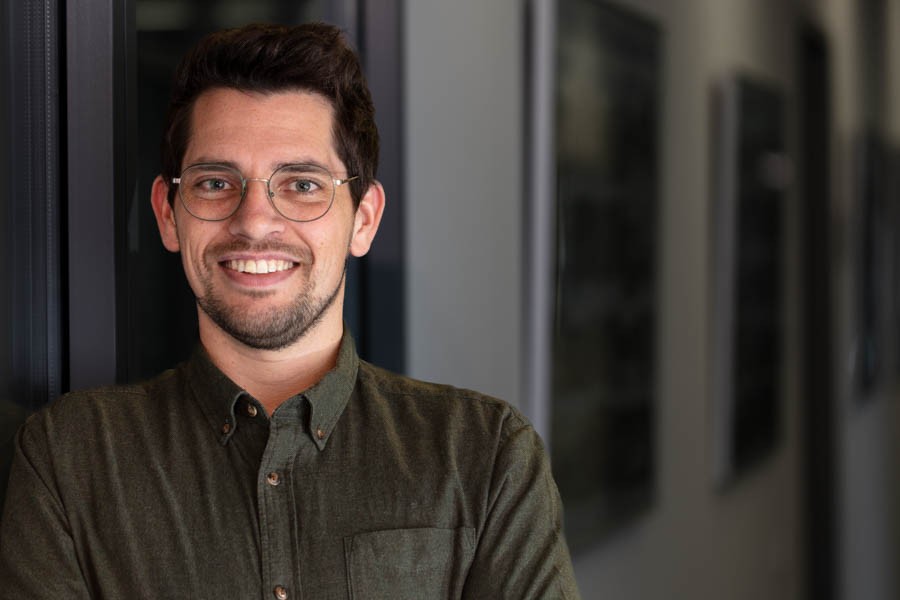
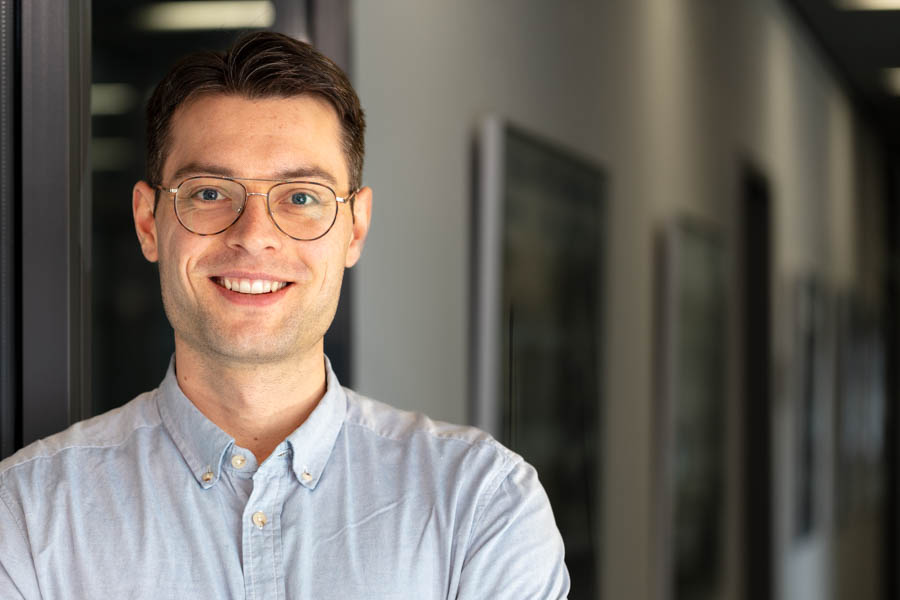
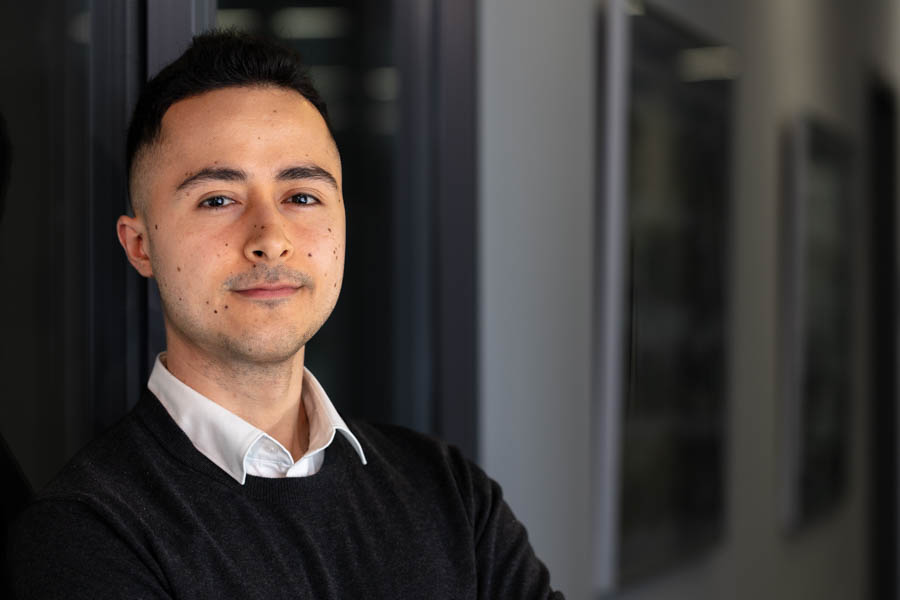
Fundings
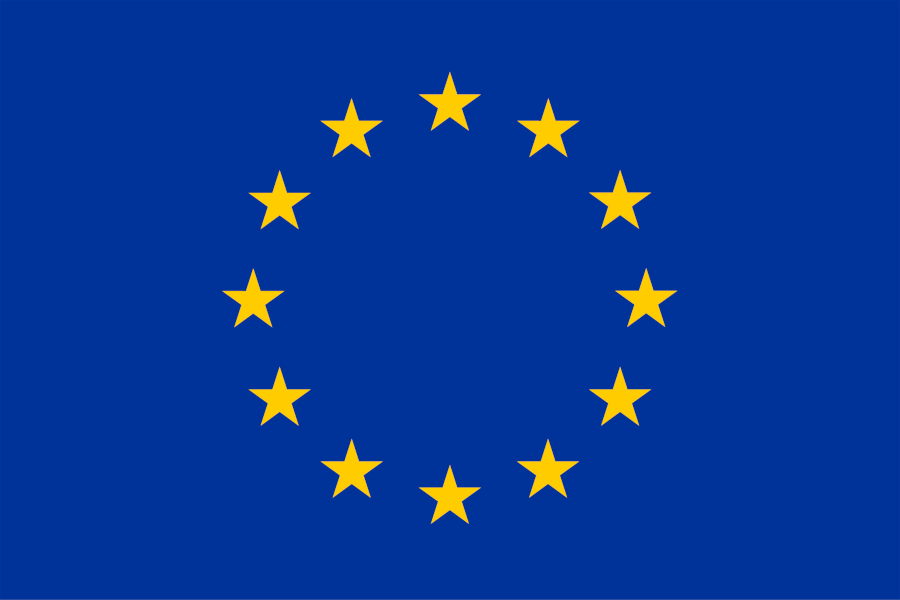
This project was funded by the European Union’s Research Fund for Coal and Steel under the Grant-ID 101099158. The funding was granted within the call Big Ticket for Steel “RFCS-2022-CSP-Big Tickets for Steel”.