TTgoesH2: IGF lead technology — Integration of hydrogen as a climate-neutral energy carrier in industrial and commercial thermoprocessing technology
Programme cooperation between the 7th Energy Research Programme of the Federal Ministry for Economic Affairs and Climate Action (BMWK) and the Industrial Collective Research (Industrielle Gemeinschaftsforschung IGF)
1 January 2021 to 31 December 2023
Project description
The overall project “TTgoesH2” is divided into the following subprojects:
- Development of ultra-low-emission combustion systems for thermoprocessing plants using hydrogen (ULoBurn)
- Industrial combustion control systems for high volatile hydrogen contents based on flame signals (GreCoCon)
- Innovative material concepts for use in hydrogen and its combustion products: Refractories, steels, ceramics for thermoprocessing equipment (ResInMa)
The IOB is directly involved in the ULoBurn and ResInMa subprojects.
Subproject 1 – ULoBurn
As part of the energy transition in Germany, efforts are being made to introduce more hydrogen generated from renewable sources into the gas transport networks. With an increased hydrogen content, the gas properties change. This poses particular challenges for the thermoprocessing industry, which primarily uses gaseous fuels. Concepts are needed for combustion systems that guarantee low pollutant emissions under varying fuel compositions, but also when using pure hydrogen. Particularly with regard to NOx-emissions, the limits are expected to be drastically lowered in the next few years. Numerous physical and chemical properties of hydrogen differ significantly from those of natural gas. This fact has serious implications for the design and development of burners, thermoprocessing equipment and their peripherals. In the field of the use of alternative fuels such as hydrogen, SMEs in the industry still have little experience, as such plants have only existed in individual cases to date. However, this knowledge is essential for the development of ultra-low-emission combustion systems for tomorrow’s thermoprocessing plants. The project aims to develop and validate concepts and recommendations for the safe and economical operation of thermoprocessing plants under the influence of hydrogen in the fuel.
Subproject 2 – GreCoCon
In many industrial high-temperature processes, the generation of process heat by technical combustion processes is still indispensable. In the course of constantly tightening emission limits, starting from large-scale plants, combustion control systems are now also increasingly being installed on smaller furnaces, which regulate the ratio of combustion air and fuel gas on the basis of the exhaust gas composition after the process, where the contact of furnace atmosphere and product has already taken place. At large industrial furnaces with sensitive processes (e.g., glass, ceramics), possible variations in fuel gas composition are detected prior to the process based on a costly analysis of the fuel. This problem will become even more acute if significantly higher fluctuations in fuel composition occur in the future. Fluctuations in the composition of natural gas can already occur today, which can lead to difficulties in the combustion process in some plants because the combustion air ratio cannot be readjusted. With an additional feed-in of high volatile fractions of hydrogen, the combustion properties change significantly and make it indispensable to use considerably more control technology in combustion processes in the future. Here, the focus must be on cost-effective and reliable systems that are available for the large number of plant types, especially for SMEs. Currently, there are no methods on the market that realize a simple, low-cost combustion control system for reacting to gas quality fluctuations upstream of or close to the combustion process, especially against the background of a future hydrogen feed into the natural gas network.
The research objective is therefore to develop low-cost, fast control systems for the fuel-air ratio based on optical signals from the flame, such as UV radiation intensity and flame lift-off.
Subproject 3 – ResInMa
In the near future, the use of hydrogen for process heat generation will affect almost all manufacturing companies. Timely preparation of existing plants and development of optimized new plants is therefore economically sensible and necessary.
The effects of hydrogen and water vapour in the furnace atmosphere and in furnace components have already been studied for some materials used in furnace construction. At high temperatures, silicate-based materials decompose under hydrogen and water vapour atmospheres. The process is dependent on the temperature and the partial pressures of hydrogen and water vapour, respectively. The damage mechanisms are largely known and investigated. In existing plants and plant concepts, these damage mechanisms were considered according to the current fuel gas compositions, or the effects could be largely ignored because they were marginal. By using pure hydrogen as fuel or fuel admixture, these concepts are no longer sufficient to guarantee a high plant lifetime, since the partial pressures of hydrogen and water vapour increase. The problem is exacerbated by enriching the combustion air with oxygen.
Companies operating in the industry are faced with several unknowns in both cases:
- Effects of hydrogen and oxygen admixture on burner operation (flame length, flame temperature, flame speed)
- Effects on furnace atmosphere (flue gas temperature, composition and velocity, dew point temperature) and refractory lining
The knowledge of these unknowns is necessary to estimate effects on materials and develop appropriate countermeasures. This is complicated by the fact that the process conditions are also subject to fluctuations due to expected variations in the fuel gas properties.
Finally, a complex test will be carried out considering all the findings from the subprojects of the “TTgoesH2” lead technology project. The findings will be summarized in recommendations for action.
Project goals
Subproject 1 – ULoBurn:
- Investigation of the resulting pollutant emissions of a precompetitive recuperator burner (with external air preheating) as a function of the air staging, the internal exhaust gas recirculation as well as during flameless combustion when using hydrogen as fuel
- Systematic investigation of the efficiency of recuperative burners when using hydrogen as a fuel, as well as the development of new concepts for increasing efficiency
- Testing of industrial recuperative burners (with internal air preheating) for different scenarios of hydrogen admixture to natural gas
- Derivation of recommendations for the retrofitting of existing plants and the construction of new plants with regard to safety technology, pollutant emissions and process windows or stability limits
Subproject 2 – GreCoCon:
- Fundamental characterization of the signal behavior of industrial sensors at high hydrogen contents in the fuel gas
- Development of control concepts based on different measurement signals, e.g. purely optical, chemiluminescence-based / combination of measurement of changes in ionization current as well as flame intrinsic glow
- Technical implementation of a combustion control system based on the developed control concepts
- Testing of the control system on industrial burners of different power classes with regard to thermoprocess and boiler applications
- Testing of the control system on H2-optimized oxy-fuel burners of subproject 1 (ULoBurn)
Subproject 3 – ResInMa:
- Experimental and numerical investigations to determine the boundary conditions
- Investigation of the influence of hydrogen on the strength of steels under cyclic thermal and thermomechanical loading
- Estimation of the influence of different damage mechanisms and reactions on refractories, ceramics and coatings
- Determination of the long-term behavior of selected materials under the determined boundary conditions under atmospheric-cyclic loading and continuous loading
- Determination and quantification of the damage caused by hydrogen and water vapor to the material samples
- Development of a material concept for the efficient use of hydrogen in thermoprocessing plants
Project participants
- Lehrstuhl für gas- und wärmetechnische Anlagen at TU Bergakademie Freiberg [Subprojects 1 and 3]
- Gastechnologisches Institut gGmbH Freiberg (DBI) [Subprojects 1 and 2]
- Gas- und Wärme-Institut Essen e.V. (GWI) [Subproject 2]
- Institute for Combustion and Gas Dynamics at the University Duisburg-Essen [Subproject 2]
- Leibniz Institute for Material-Oriented Technologies (IWT) [Subproject 3]
Further Informationen
Contact
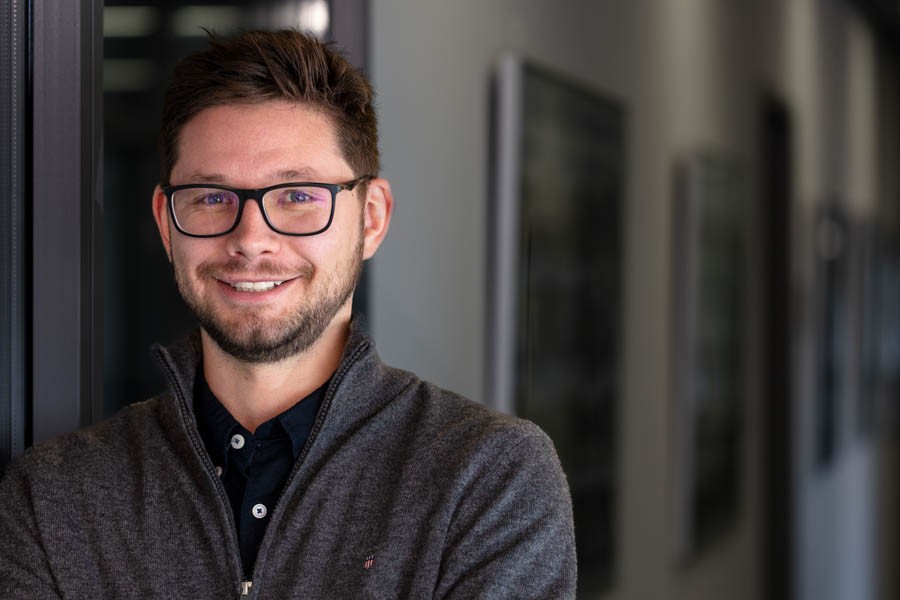
Funding
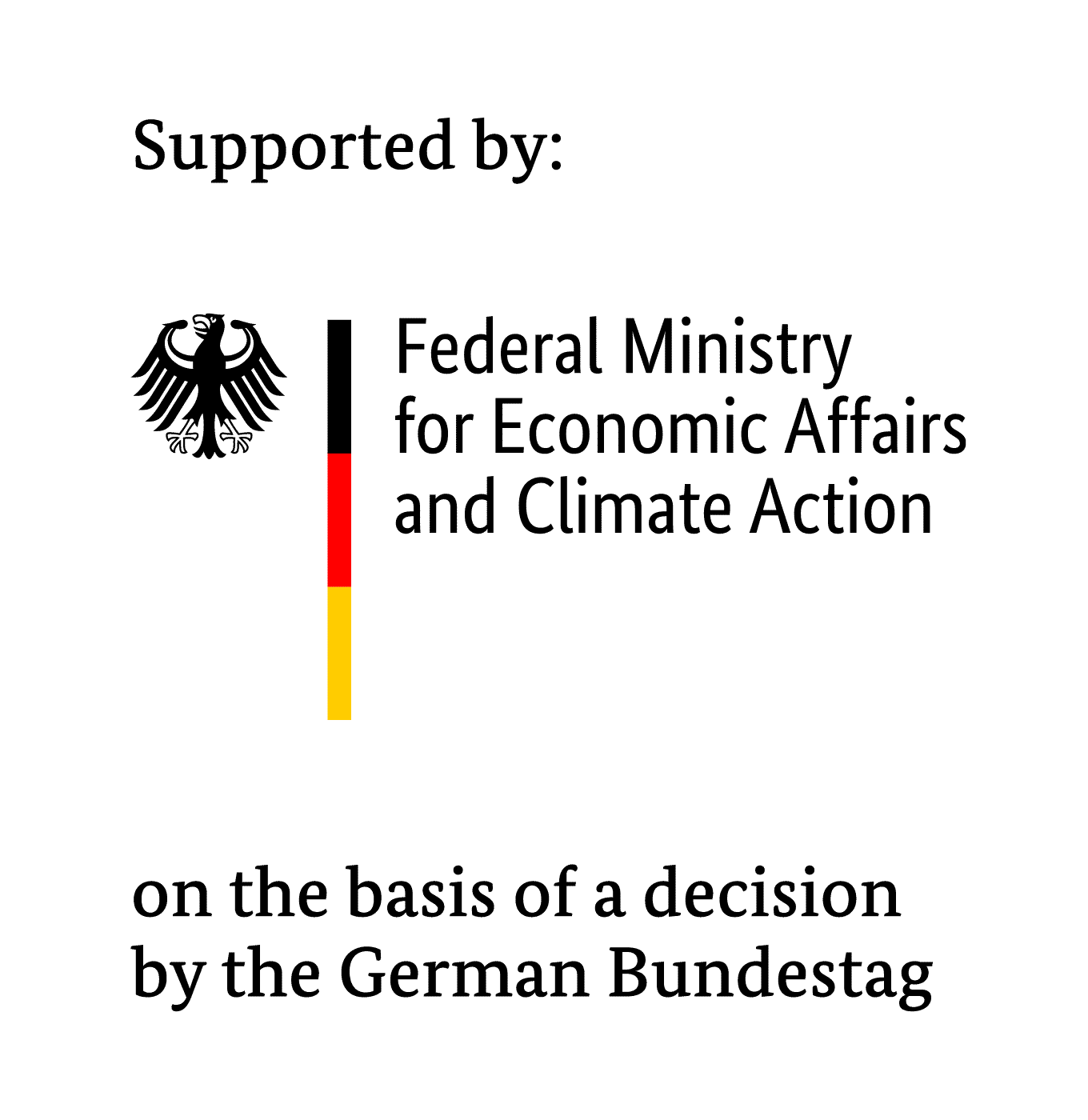
These projects are funded by the Federal Ministry of Economic Affairs and Climate Action (BMWK) on the basis of a decision by the German Bundestag.
IGF project no.: 31 LBG (ULoBurn) and 33 LBG (ResInMa)