Development of novel resistance heating elements through innovative material and process combinations
Industrial Collective Research (IGF), 1 April 2024 to 31 March 2026
Project description
In 2020, the demand for natural gas as an energy source in industry was 324 TWh, which corresponds to 31% of Germany’s total demand. With a planned reduction of 55% in greenhouse gas emissions in 2030 compared to 1990, the conversion of gas-fired heat treatment plants to alternative heating methods is unavoidable in the long term. Added to this is the pressure on industry resulting from increased primary energy costs and a prospective reduction in dependency on the fossil fuel market.
Switching to electric heating systems with electricity from renewable sources enables the greatest possible reduction in CO2 emissions, even compared to hydrogen heating. In addition, electric heating does not cause any direct CO2 emissions during production, which saves companies the cost of CO2 certificates and improves their competitiveness in international competition. The flexible geometric customisation options of electric heating elements are also advantageous. Industrial furnace construction companies, service providers for automation and process modelling as well as companies outside the metalworking industry in particular would benefit from the conversion of the heating system.
In some fields of application, such as vacuum furnaces in batch operation, electrical heating systems with resistance heating elements are already established. In many systems (e.g. roller hearth furnaces), however, resistance heating elements are not available or not yet established due to the requirements placed on the systems. The mechanical stress on the heating elements is particularly problematic.
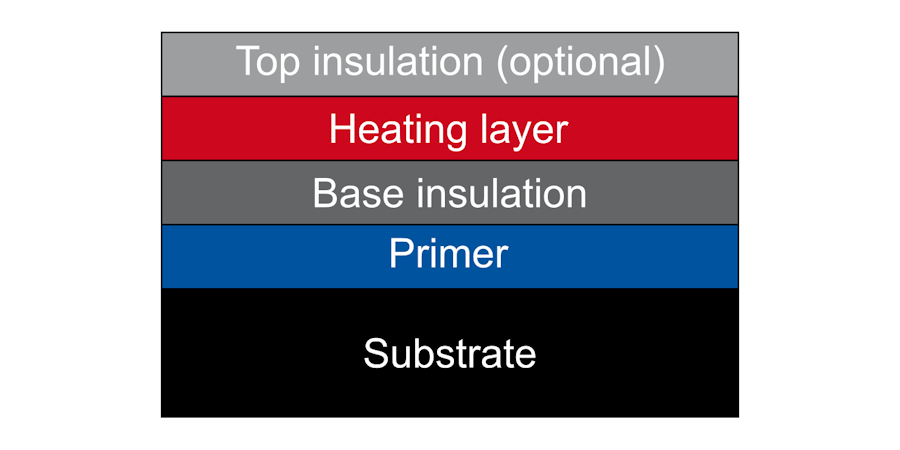
Schematic structure of a heating layer system
The aim of the research project is therefore to develop a new type of heating element that fulfils the process requirement for mechanical stability while at the same time providing sufficient and uniform heat input into the process. Thermal spraying (TS) is a promising method for manufacturing these heating elements. TS enables thin, flat layers to be applied to a metallic or ceramic substrate. Overall, the heating element applied by thermal spraying (see illustration) is a layered system consisting of two insulating layers and a conductive layer in between. The layer that is exposed to the mechanical load can be made of a chemically and mechanically resistant material. Although the first successful applications of TS already exist, e.g. in aluminium casting, the use of TS heating systems in thermal process technology has not yet been carried out or scientifically investigated. In particular, questions regarding the maximum possible heat input per surface, the electrical contacting for a heating profile that is as homogeneous as possible or the chemical and mechanical resilience in the intended area of application are still open. This includes temperatures up to 1150°C and different atmospheres, which are derived from the potential applications mentioned.
Project goals
- Carrying out a materials engineering design of thermally sprayed heating layer systems as a function of different operating temperatures and atmospheres
- Development of contacting concepts for different heating layer materials, furnace atmospheres, operating modes and temperature ranges
- Determination of the maximum power density taking into account different operating conditions (temperatures, atmospheres)
- Possibilities of integrating the heating layer systems into existing thermal processing systems and evaluation of possible concepts for new systems
Project participants
Further Information
Contakt
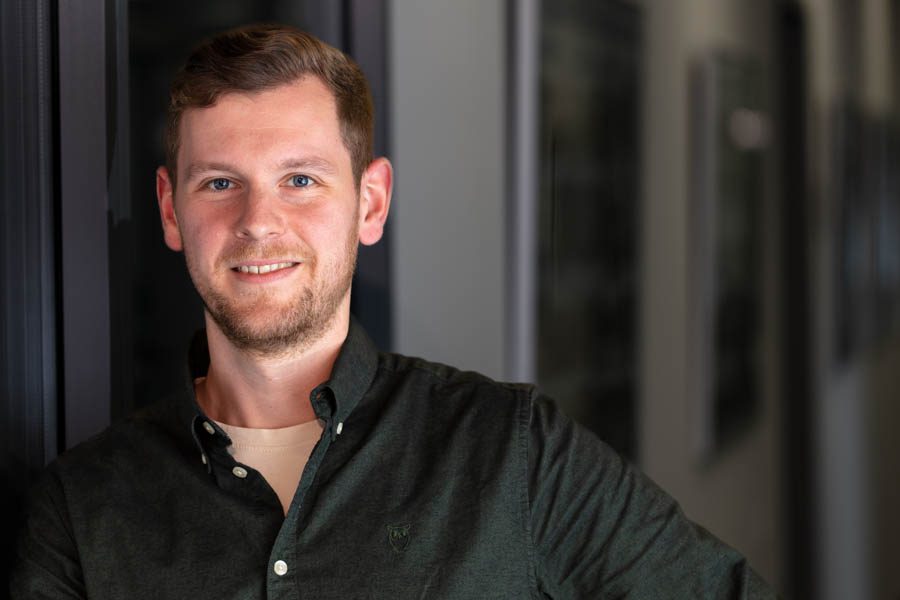
Funding
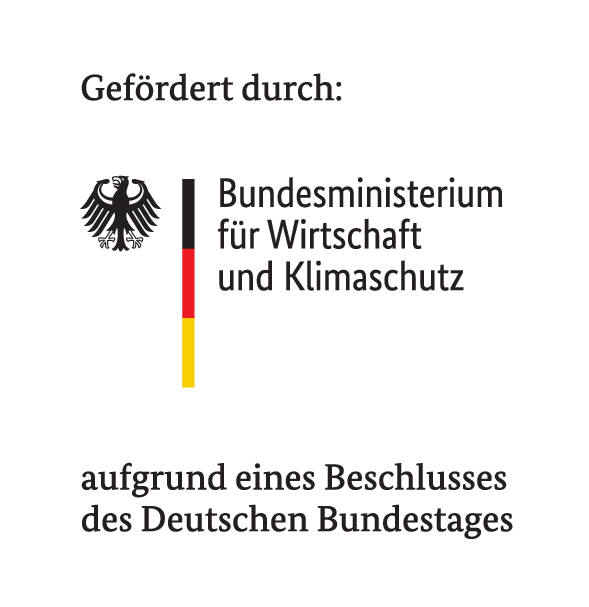
The project (project no. 23062N) was submitted with the support of the Research Association of Industrial Furnace Manufacturers (FOGI) via the Forschungskuratorium Maschinenbau e.V. (FKM). It is funded via the German Federation of Industrial Research Associations „Otto von Guericke“ (AiF) in the program for Industrial Collective Research (IGF), initiated by the Federal Ministry for Economic Affairs and Climate Action due to a resolution of the German Bundestag.
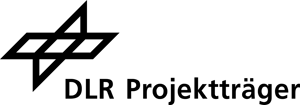
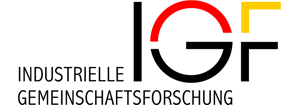
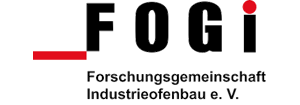