Project description
The development of an innovative and energy-efficient annealing line is the goal of the HeatSteel project, with the aim of improving process stability in the production of thin precision strips with regard to product quality. Existing continuous lines for the annealing of precision strips have not been significantly developed in the last decades with regard to their energy efficiency and product quality. By developing a new plant concept and building an innovative pilot plant, the energy utilisation can be optimised in the future and the product properties improved.
In the course of the project, a furnace model is being developed at the IOB that can calculate the process in the innovative hardening furnace including the cooling unit. In addition to describing the strip temperatures at each point in the production process, the process model will also simulate the mechanical strip behaviour in the plant. Based on experimental cooling tests on a test rig at the IOB, a study will be carried out to develop a deformation-optimised cooling unit using simulations.
Based on the investigations, the cooling unit of the new plant will be designed together with the project partners and subsequently used in the industrial annealing line.
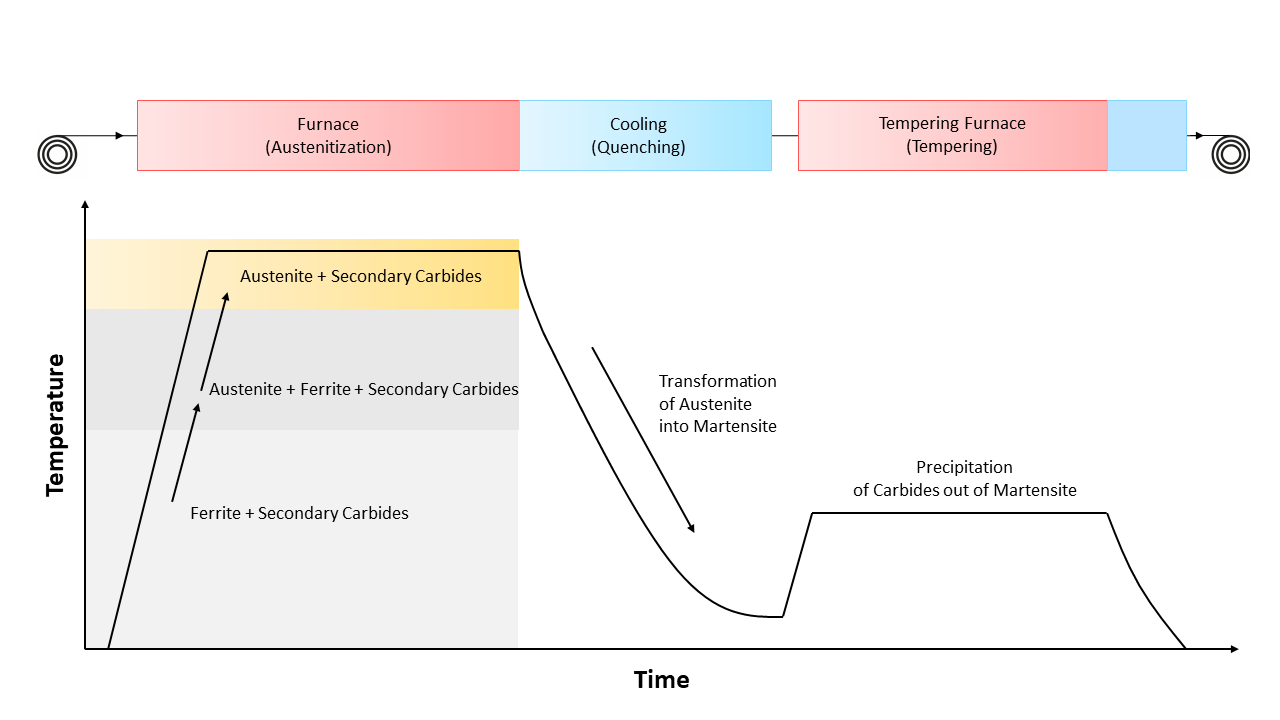
Temperature profile for the annealing of steels
To achieve and validate the necessary process stability, a control system based on the process model and an AI-based process monitoring system will be implemented in the new plant.
Project goals
The aim of the HeatSteel project is to develop an innovative and energy-efficient annealing line for thin stainless martensitic precision strips. At the same time, in the course of developing an energy-efficient line, the extent to which process stability can be improved in terms of product quality is to be examined.
The project will develop a new plant concept for the continuous annealing of precision strips. The heart of the plant will be the innovative hardening furnace including cooling unit as well as the necessary sensor technology and model-based controls for controlling the process parameters. In addition, AI-based process monitoring and quality optimisation will take place.
Energy efficiency is to be achieved through the following strategies:
- New arrangement of elements in order to use the waste heat from the hardening furnace specifically for the hardening process itself or for the tempering process.
- Better insulation and thus reduction of energy losses.
- Increase in output and thus more efficient use of raw materials.
The new line and the expected savings are expected to reduce carbon dioxide emissions by 760 tonnes in 2025. The construction of a first production line with testing as well as validation of the plant concludes the project.
By participating in this project, the IOB is expanding its competences in the area of plane position simulations as well as general process modelling. Thus, a transfer of the modelling approaches to strip processing lines for other materials and steels in the area of higher throughputs will be possible in the future. Furthermore, the understanding of control-relevant manipulated variables is increased so that future process models can also be used for control optimisation.
Project participants
- In cooperation with a manufacturer of precision strip based in North Rhine-Westphalia
- WSP GmbH
- Fraunhofer Institute of Optronics, System Technologies and Image Exploitation IOSB
- Industrial Automation branch INA of Fraunhofer IOSB
Contact
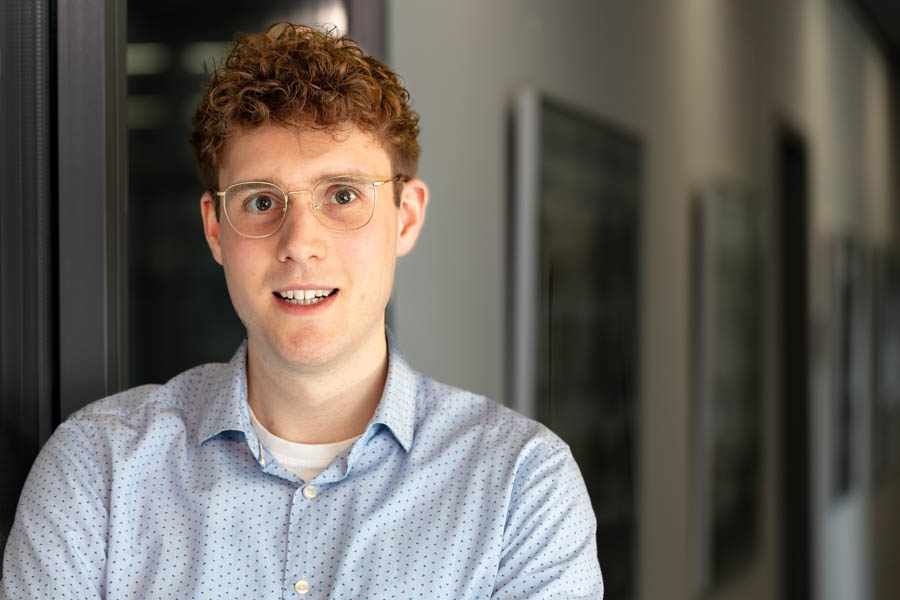
+49 241 80–25939
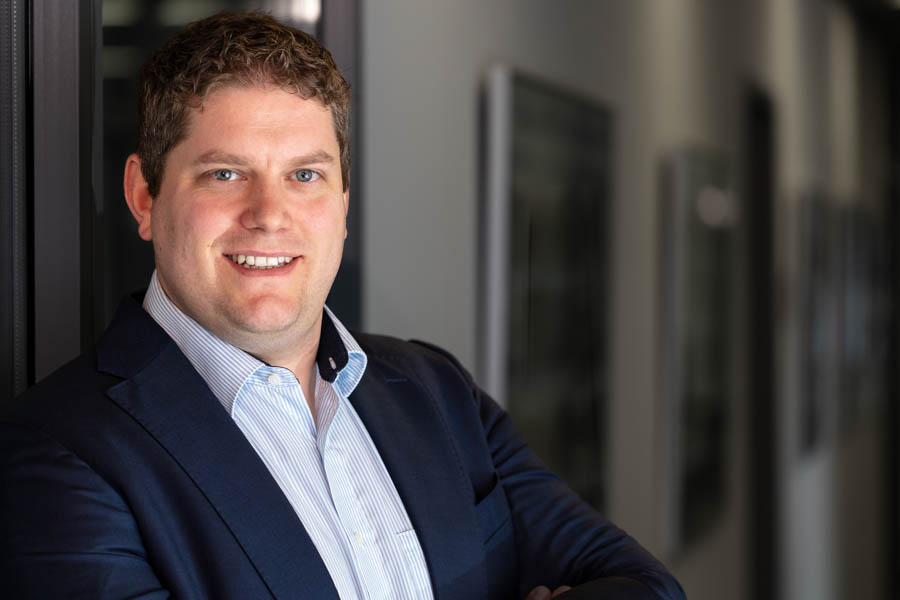
+49 241 80–26065
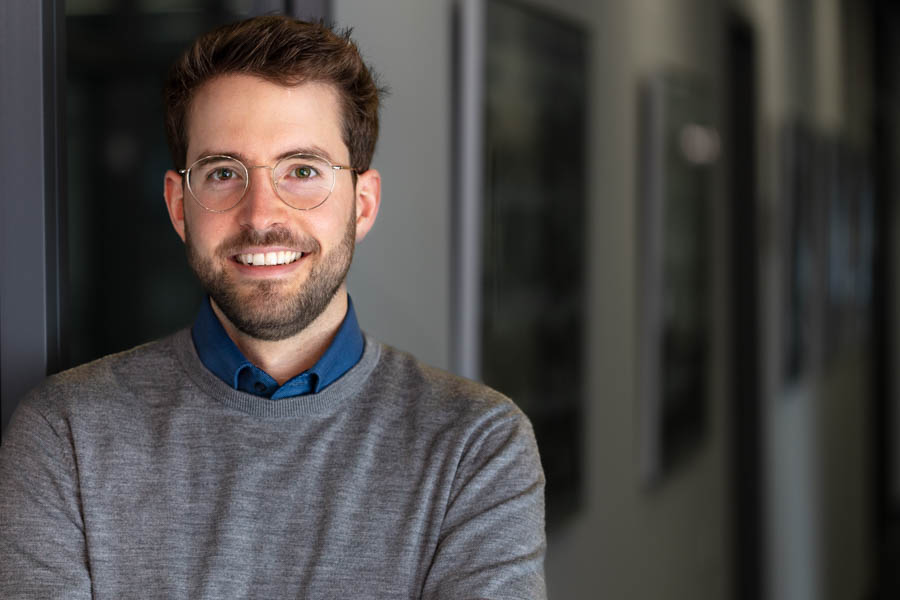
+49 241 80–26067