Investigation of the influence of flexible operating modes of industrial furnaces on the service life of metallic high-temperature components
The German Federation of Industrial Research Associations „Otto von Guericke“ e.V., Industrial Collective Research (AiF IGF): 1 July 2020 – 30 June 2024
Project description
The productivity and reliability of thermoprocessing plants are of decisive importance for their operators and manufacturers. In the context of the energy transition in Germany, the goal of sustainability for society as a whole is becoming increasingly important. Strategies for plant maintenance are evolving from reactive and preventive measures to predictive, condition-oriented functional maintenance. This applies in particular to energy-intensive plants, for example for the heat treatment of metals.
High-temperature loaded components in industrial furnaces experience accelerated creep deformation under thermal cycling compared to isothermal loading, which in combination with corrosive damage limits the service life of these components. One example of such components are radiant tubes, which are used for indirect heating in industrial furnaces in which inert gas atmospheres are used. At the end of their service life, the radiant tubes are no longer functional due to cracks or severe deformation (see Figure 1) and the tubes have to be shut down. The reduced power input decreases the productivity of the furnace until the tubes are eventually replaced during a plant shutdown. The replacement results in direct costs for new radiant tubes, as well as indirect costs due to the lost production capacities. The increase in component service life thus represents a significant optimization potential for plant operators.
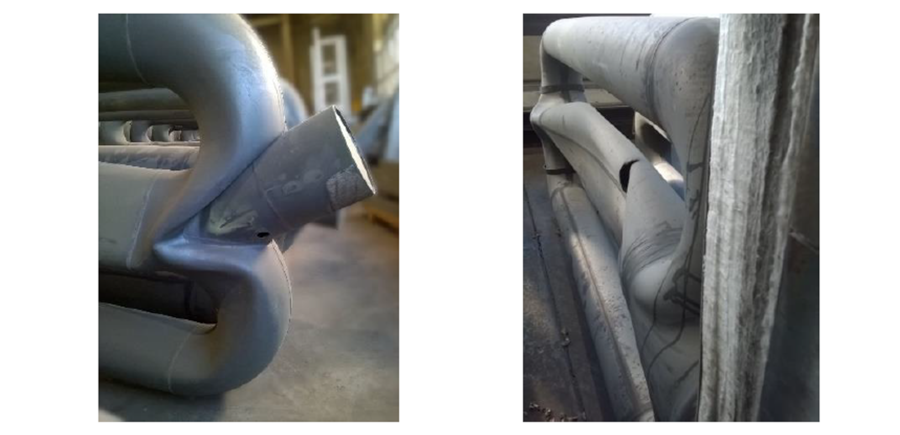
Figure 1: Double-P-type radiant tubes at the end of their service life
The aim of the research project is to investigate the influence of flexible furnace operation on the service life of metallic high-temperature components. In the course of the project, a mathematical model will be created to describe the creep deformation and material damage of selected materials, which will subsequently be used in numerical models to calculate the deformation of various radiant heating tubes under the action of different temperature cycles. A novel, mechanism-based creep model is being developed with experiments on uniaxially loaded creep specimens at the Institute for Materials Science (IfW) at TU Darmstadt. The research institute OWI Science for Fuels gGmbH (OWI) is investigating the chromium evaporation rate of material samples under combustion atmospheres in corrosion tests, with which the material model is being extended to include a term for material damage. Also, the experiments are transferred here to a more complex stress situation in the form of beam specimens supported on one side in long-term tests.
At the Department for Industrial Furnaces and Heat Engineering, the experiments are being extended to single-ended radiant tubes (SER) as an example of high-temperature components. For this purpose, a new test rig (Figure 2) is being set up for the project, in which radiant tubes are loaded with different temperature changes in long-term tests. The setup is equipped with process control technology based on industrial standards. A modular design allows the installation of different radiant tube geometries and thus enables long-term use of the test rig. After the tests, the tubes are measured three-dimensionally to evaluate the deformation of the tubes.
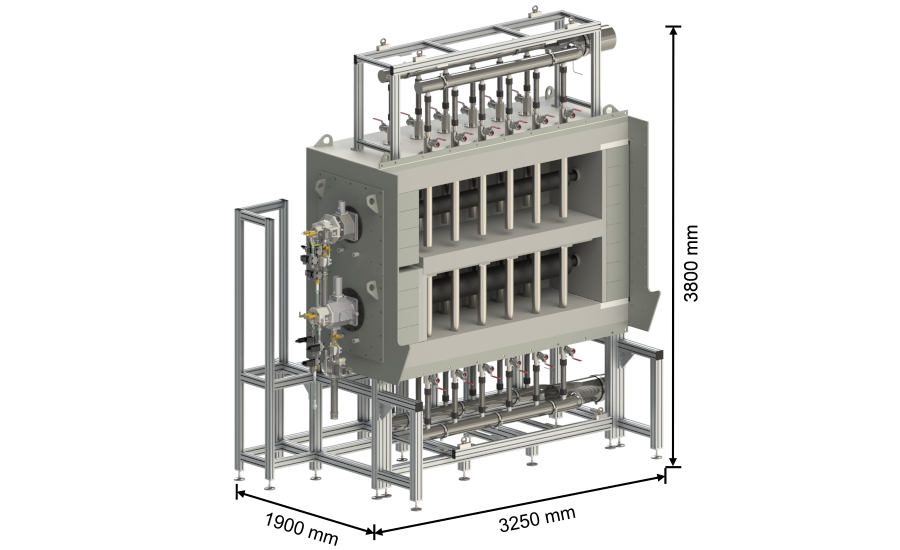
Figure 2: Modular test rig with two single-ended radiant tubes
Numerical models developed during the project and validated with the test results of all project partners, enable the findings from the experiments to be transferred to more advanced load cases. A two-stage simulation process is followed for the calculation of the radiant tube lifetime: Numerical flow simulations are used to calculate the transient temperature distribution of a radiant heating tube (Figure 3). The results are then transferred to structural simulations in which the transient deformation of the radiant heating tube is calculated using the developed material model.
Figure 3: Exemplary results from a transient numerical simulation: SER temperature profiles during burner on-off-firing
Finally, the numerical models are used to set up investigations for various industrial application scenarios. The resulting comprehensive database on common high-temperature materials and radiant heating tubes enables plant operators to optimize the operation of their plants with regard to the service life of installed components.
Project goals
- Identifying recommendations for optimizing the operation of industrial furnaces to optimize the service life of high-temperature components, taking into account production engineering framework conditions and energy efficiency.
- Development of a material model with descriptions of the creep and corrosion behavior of selected materials
- Development of a numerical modeling approach for the calculation of creep deformation of high-temperature components
- Identification of microstructural mechanisms contributing to accelerated creep deformation during temperature cycling
- Development of a minimal test program by means of Design of Experiments for the transfer of the material model to further materials
Project participants
Contact
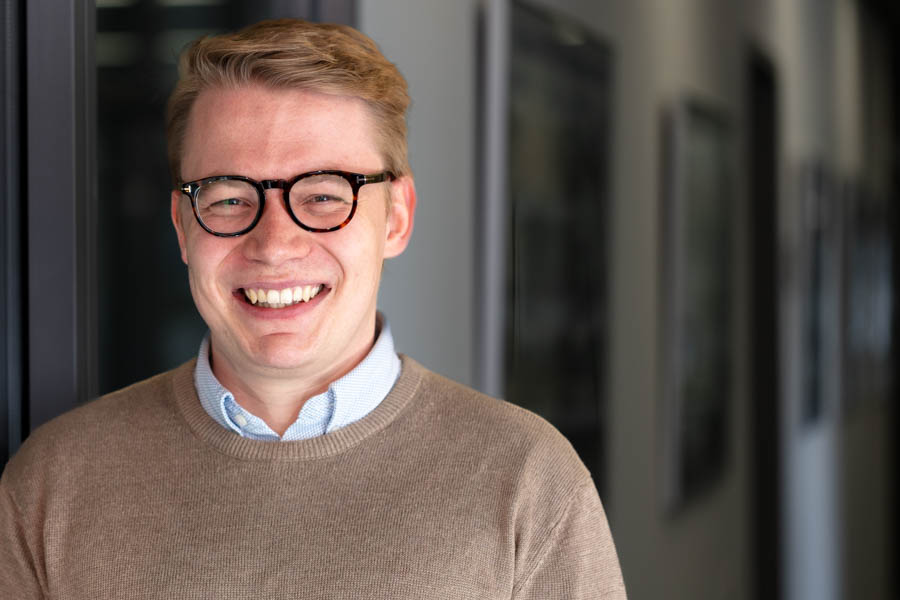
Funding
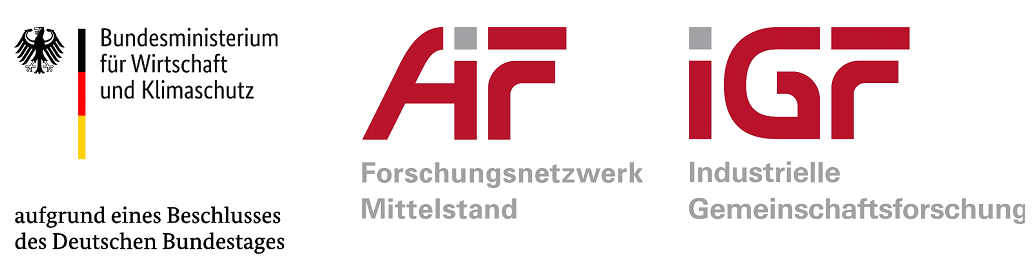
This project is supported by the Federal Ministry for Economic Affairs and Climate Action (BMWK) on the basis of a decision by the German Bundestag.
IGF-Project-No.: 21070N