Coupled Process Chain Modeling
Industrial Collective Research (IGF), 01. June 2021 to 30. November 2023
Project description
In the project, the semantic interoperability of mathematical process models between individual steps of the process chain is to be improved. To this end, model extensions and a platform for data management as well as for the uniform execution of the models will be developed and validated in the industrial production of aluminium and copper flat products. A special focus is on the description of interfaces and data formats and the use of semantic annotations.
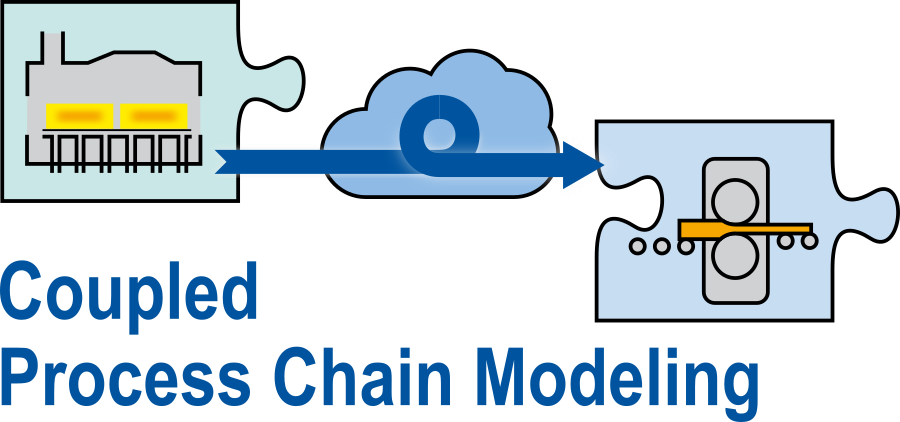
Logo of the IGF project
The basis lies in the dependence of the properties of metallic and semi-finished products on the entire chain of processes passed through during manufacture. The mechanical properties such as tensile strength, hardness and toughness are influenced not only by the alloy composition but also by the degree of forming and the temperature-time profile in the preheating and heat treatment processes. The current properties of the product also have an inverse effect on the parameters of the process being run through. The required forces and maximum forming degree per forming step are dictated by the current mechanical properties. The heat transfer within the furnace is in turn dependent on the current product geometry.
Mapping of these complex and multidimensional dependencies between process parameters and product properties has so far been considered in industrial practice only for individual processes and not over the entire process chain. In industrial practice, process data from the previous processes is usually available when planning and executing downstream processes. Aggregates for individual processes are increasingly equipped with mathematical process models. Among other things, they serve as soft sensors and determine values that are not accessible with measurement methods and predict values that will occur in the future when a control scenario is applied. The knowledge gained can be used for model-predictive control as well as conventional control, for batch planning, when considering properties like quality and energy savings. In forming processes, such models are used, for example, for the design of thermomechanical processes, calculation of the temperature via a rolling process or height-resolved grain size prediction.
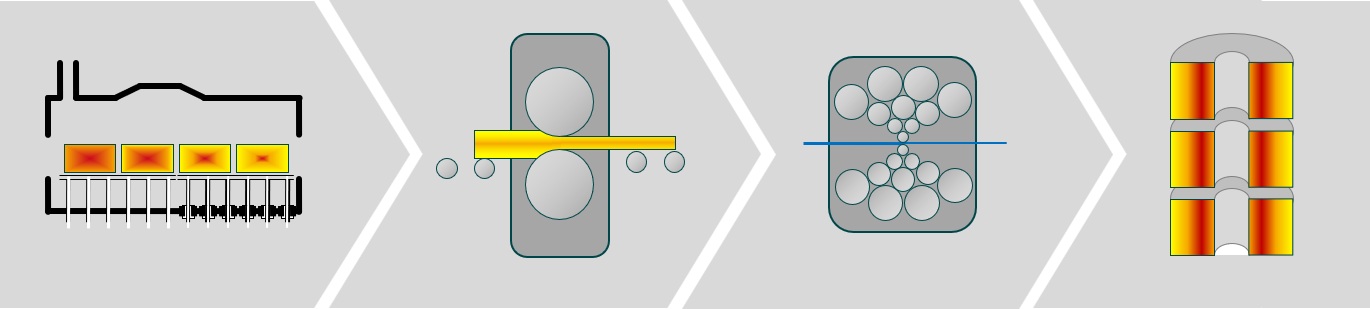
Exemplary process chain
The exemplary process chain for strip material shown in the figure may contain a process model for each individual aggregate, which has been adapted from years of industrial use. With the use of such models or modelling strategies, besides the consideration of the product properties, an analysis of the energies and resources used for each individual process is possible. The problem, however, is that in industrial practice, once generated, data is usually not available to process models of other plants, although these data is valuable as initial conditions and parameters for models of processes downstream in the process chain. Models that are supplied as part of a plant and/or have been created or supplied to address specific issues within a production process are generally not designed to be used in an overarching view across multiple processes. The models sometimes contain extensive information about processes and, if they are updated or trained manually and/or automatically with information from production, have been improved and optimized over years in some cases.
Together with the IBF and the IAT of the RWTH Aachen University, the IOB strives to couple the individual process models via a suitable platform for data management. The data exchange is intended to improve the accuracy of the process models and thus achieve energy and resource savings and quality improvements in the processes. Defined interfaces and data semantics are intended to simplify the integration of heterogeneous models in particular.
Project goals
- Establishment of a platform for data management, storage, transfer and uniform execution of model calculations
- Independent of technology and manufacturer of the models
- Independent of the material
- Independent of software solutions used by the organizational unit
- Extension of existing process and material models for integration into a data platform
- Model validation on industrial demonstrators:
- Production of aluminium sheets for the manufacture of beverage cans
- Production of copper sheets
- Use of process chain modelling to adjust intermediate annealing and simultaneously optimize rolling processes to
- Reduction of the tail formation in the deep drawing process and the improvements in the achievement of the final properties
- Increase of energy efficiency
Project participants
Further Information
Contact
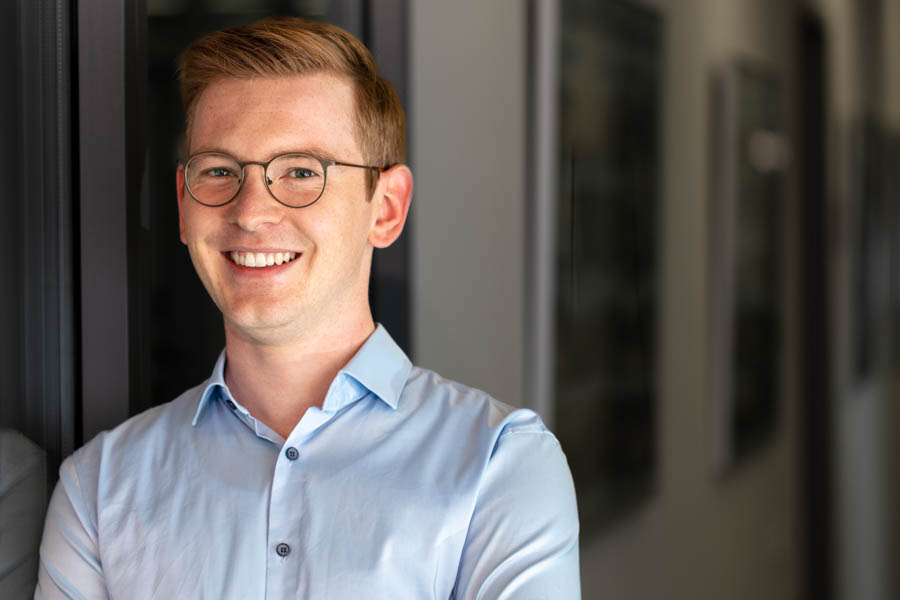
Funding
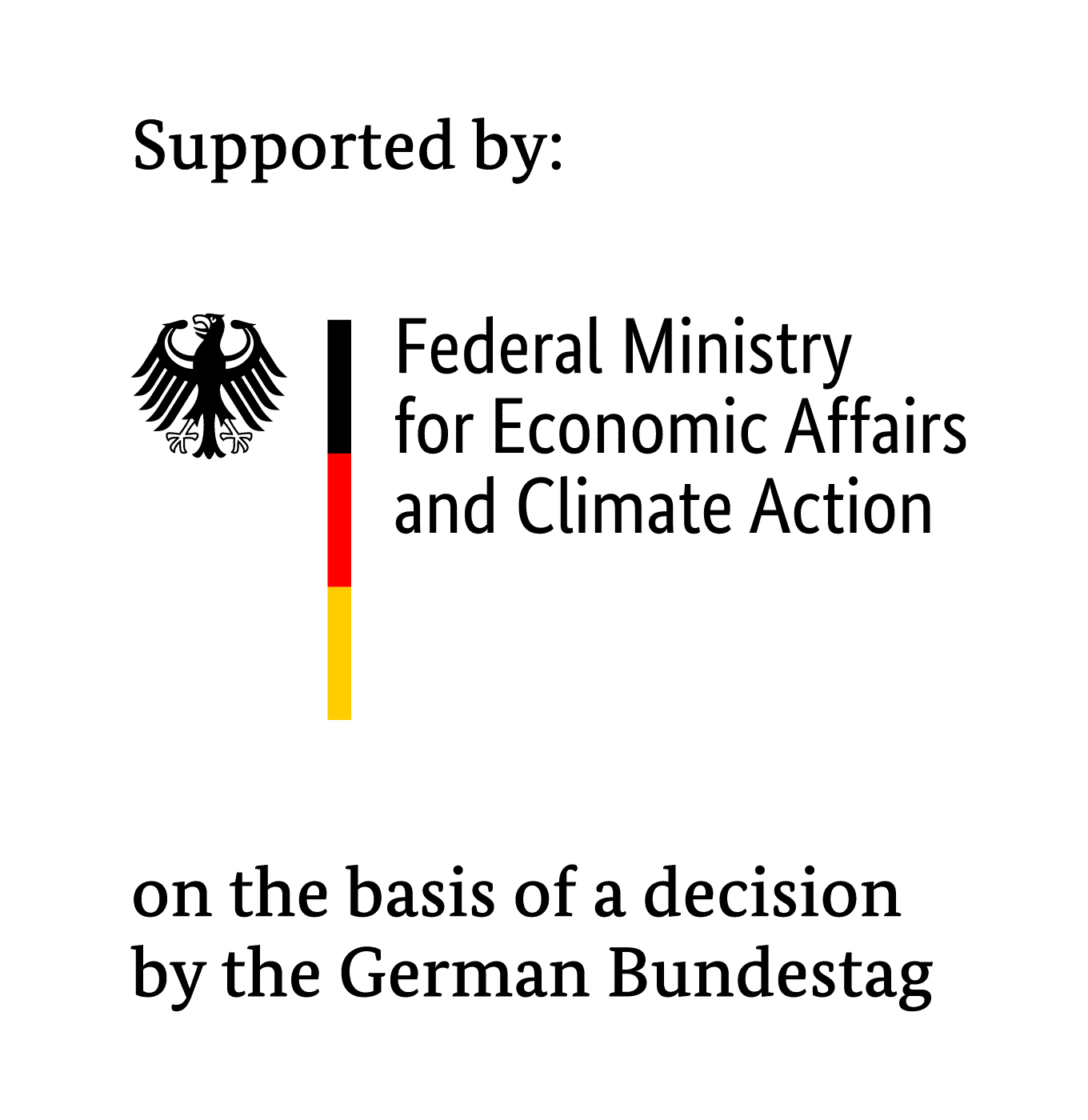
The project (project no. 21884 N) was submitted with the support of the Research Association of Industrial Furnace Manufacturers (FOGI) via the Forschungskuratorium Maschinenbau e.V. (FKM). It is funded via the German Federation of Industrial Research Associations „Otto von Guericke“ (AiF) in the program for Industrial Collective Research (IGF), initiated by the Federal Ministry for Economic Affairs and Climate Action due to a resolution of the German Bundestag.