The IOB operates a pilot-scale electric arc furnace in the Technology Park Herzogenrath (TPH).
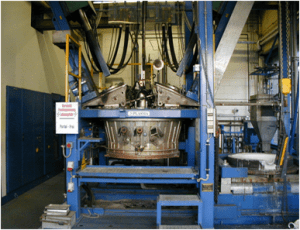
The bottom vessel of the electric arc furnace has an effective capacity of approx. 40 litres, which corresponds to approx. 200 kg of liquid steel. Depending on the condition of the brick lining, the height of the bath in the vessel is thus about 10 to 15 cm.
The maximum active power is 600 kW with a maximum arc current of 2000 A. The system can be operated either in DC or AC mode with one electrode and one bottom electrode inserted in the lower vessel or with two electrodes in AC mode. In addition, the design of the system permits the use of drilled graphite electrodes in direct current operation on a scale relevant to the operational application.
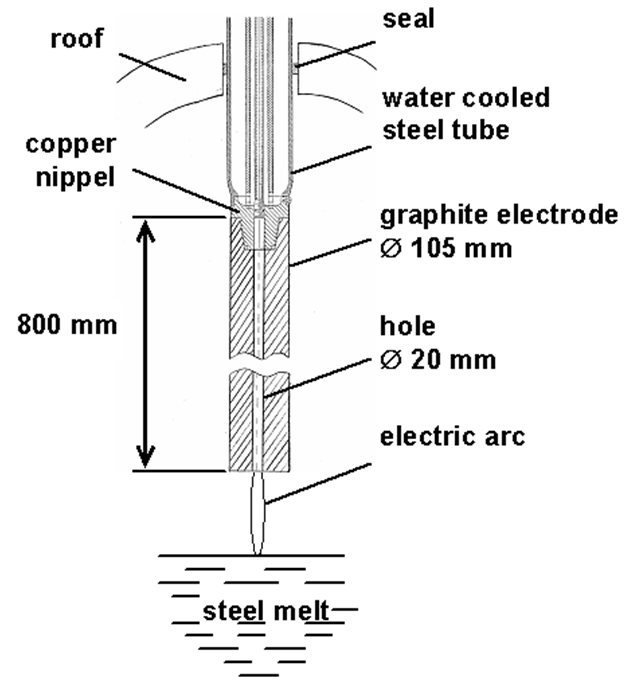
Alternatively, the arc furnace can be operated with plasma torches. A melting furnace equipped with plasma torches is particularly suitable for the investigation of metallurgical effects since, in contrast to graphite electrodes, gas-tight furnaces are possible with water-cooled metal torches. The main electrodes consist of thorinated tungsten. Between them and the bath, arcs stabilized with argon are generated.
The furnace chamber is sealed gas-tight by pneumatic seals, so that the atmosphere can be selected almost at will. A ring line around the furnace allows lateral injection of any additional gases, the injection rate of which is adjusted by means of mass flow controllers. An exhaust gas analysis system is available for continuous analysis, monitoring and recording of the gas atmosphere during the tests. The complete melting plant is water-cooled.
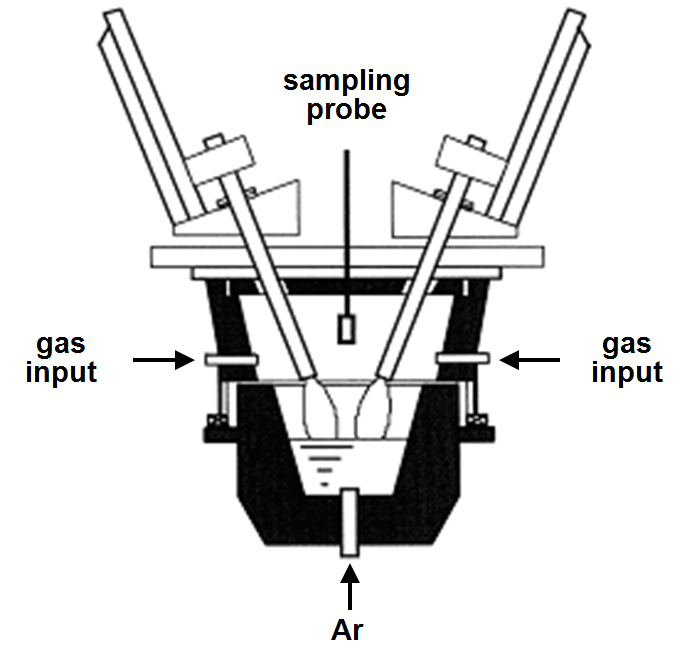
The furnace can be equipped with one (alternating current operation) or two (direct current operation) porous plugs installed in the crucible bottom, so that thermal and chemical homogenisation of the melt by stirring is possible.
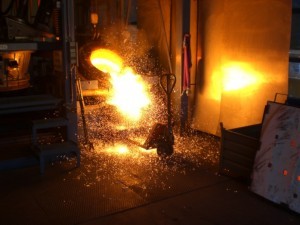
For process control, a measuring and control unit with a programmable logic controller (PLC) is installed as the core, which contains display instruments, operating elements and monitoring equipment required for safe operation. Various functions (current, gas consumption, cooling water temperature, etc.) are monitored and/or controlled simultaneously.
A system for recording, storing and evaluating the measurement data is installed for the documentation of the tests. This system documents parameters such as power inputs, temperatures, pressures and flow rates.