Spray nozzle fields in cooling sections: Defined setup of heat transfer profiles in spray nozzle fields for optimization of heat treatment in continuous strip plants
Industrial Collective Research (IGF), 1 August 2019 to 31 July 2023
Project description
As part of the industrial production of high-strength metallic materials, they have to necessarily undergo a heat treatment to set the desired mechanical properties. In the case of flat products, this heat treatment is usually carried out in continuous plants which always include a cooling stage. During this process, the cooling rate has a decisive influence on the resulting microstructure and thus on the mechanical properties. Especially in the field of high-strength materials (e.g. age-hardenable 7XXX aluminium alloys), a particularly high cooling rate is required, which can only be achieved by water cooling. For this purpose, the water is dispersed into droplets via spray nozzles and applied to the surface of the material. In continuous plants, arrays of spray nozzles are used for this purpose, in which the spray areas of the individual nozzles overlap. As a result, complex flow phenomena (water mountains, etc.) form on the surface, which influence the heat transfer and cooling rate. Therefore, the flow phenomena and their influence on the heat transfer are investigated in the project “Spray nozzle fields in cooling sections” in order to adjust the heat transfer on the surface in a defined way afterwards. The flow phenomena are determined at the Department for Industrial Furnace and Heat Engineering. The heat transfer coefficients are determined at the Chair of Thermodynamics and Combustion at Otto von Guericke University Magdeburg. Subsequently, the results of the two project partners will be correlated in order to determine the influence of the relevant parameters.
To realise this objective, several test rigs have been set up at the Department for Industrial Furnaces and Heat Engineering as part of the project. With the first test rig, the flow on a stationary horizontal surface below any given nozzle field can be investigated.
In the course of the project, a furnace model is being developed at the IOB that can calculate the process in the innovative hardening furnace including the cooling unit. In addition to describing the strip temperatures at each point in the production process, the process model will also simulate the mechanical strip behaviour in the plant. Based on experimental cooling tests on a test rig at the IOB, a study will be carried out to develop a deformation-optimised cooling unit using simulations.
Based on the investigations, the cooling unit of the new plant will be designed together with the project partners and subsequently used in the industrial annealing line.

Test rig for determining the flow in a nozzle field on a stationary horizontal surface
For this purpose, different measurement methods are used, some of which were developed within the scope of the project. For example, the flow formation can be optically quantified with a camera. In addition, an investigation with ultrasonic sensors or force sensors is possible. These sensors can be used to determine both the characteristics of the flow and the resulting impact momentum of the water droplets. The test rig has also been extended to include the possibility of measuring the impingement density of a nozzle or a nozzle field using a patternator. The self-constructed patternator consists of more than 1000 individual measuring points, which are automatically evaluated with the help of a respective set-up.
To ensure that the results obtained can be transferred to industrial practice, the influence of the strip speed on the flow formation is also investigated with another test rig. For this purpose, a metallic strip is continuously run over two rollers at strip speeds similar to those used in industrial applications. The strip width ranges up to one metre. The same measuring methods for determining the flow are used on this test rig.
At the same time, a test rig at the Chair of Thermodynamics and Combustion at the OvGU Magdeburg was modified in order to enable the determination of the heat transfer coefficient during the cooling of horizontally moved samples. In both Aachen and Magdeburg, identical nozzles and boundary conditions are used in all investigations. In this way, a correlation of the obtained results is possible.
Project goals
- Development or further development of methods for quantifying the flow (e.g. by optical measurement methods or the impact momentum)
- Construction and start-up of a test rig to determine the flow characteristics on a circumferential strip under variation of the process parameters
- Investigation of the local and integral heat transfer under variation of the process parameters
- Correlation of the results of both project partners and elaboration of the influence of the process parameters on flow and heat transfer
- Development of recommendations regarding advantageous process parameters with regard to a homogeneous heat transfer over the strip width
Project participants
Contact
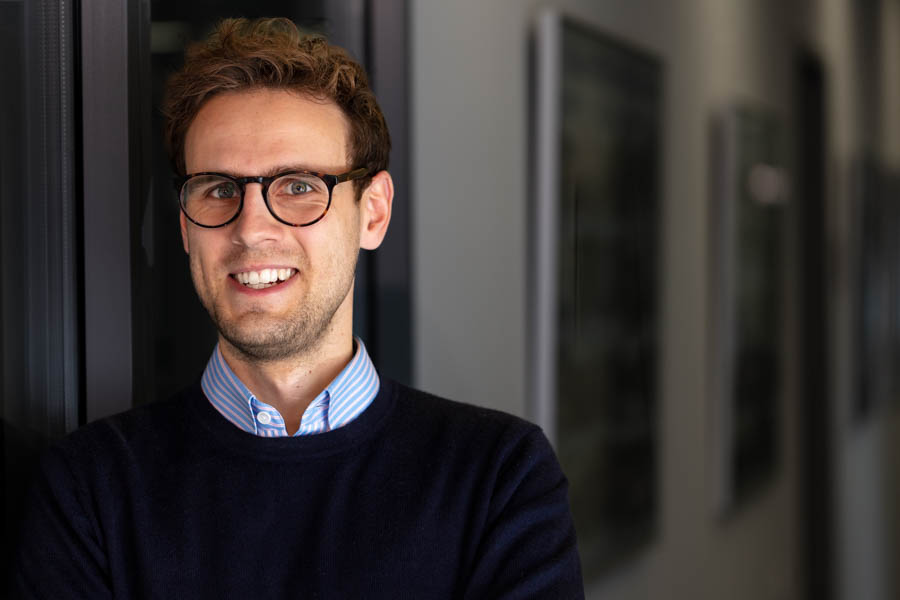
Funding
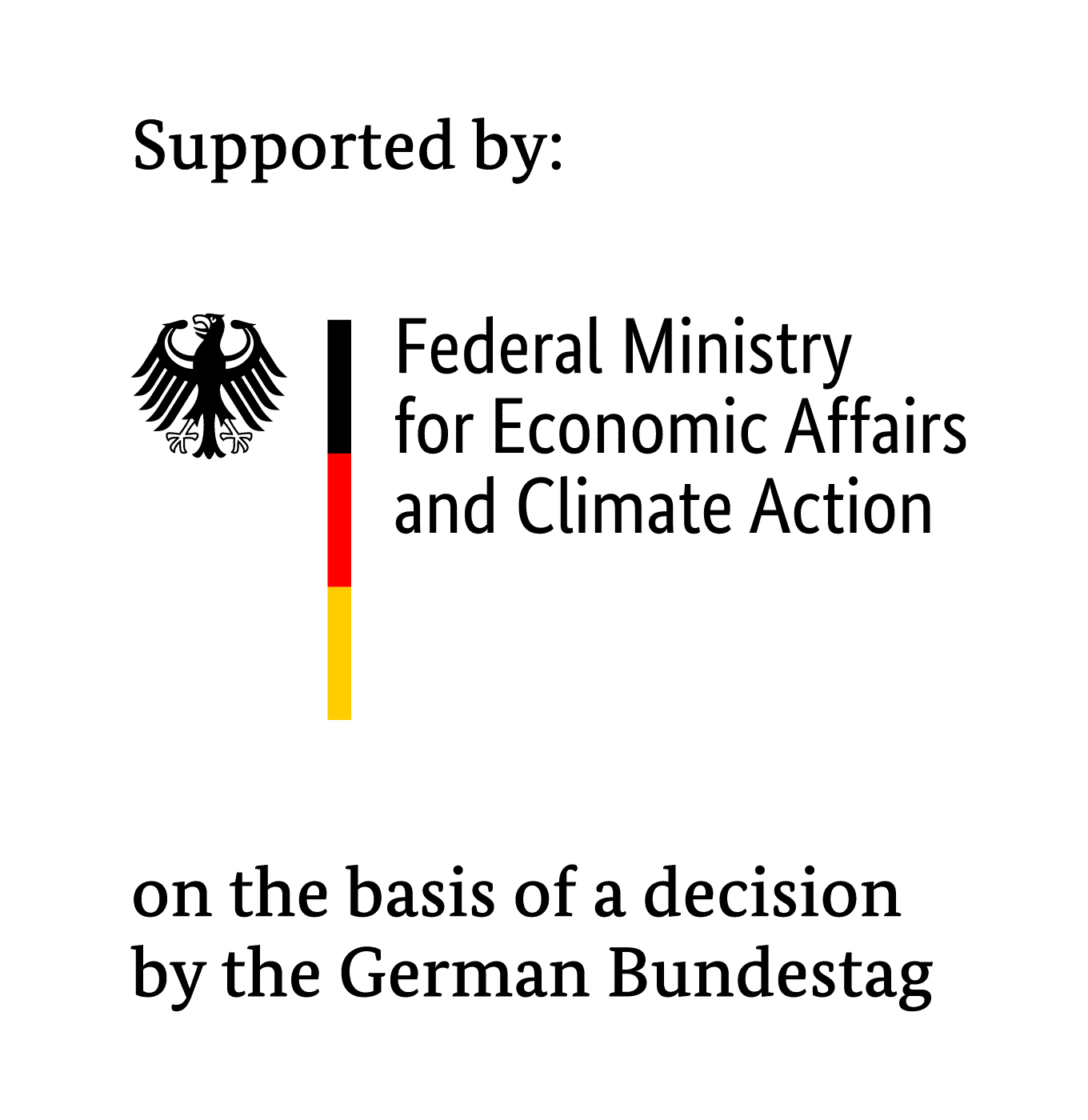
The project (project no. 20782 BG) was submitted with the support of the Research Association of Industrial Furnace Manufacturers (FOGI) via the Forschungskuratorium Maschinenbau e.V. (FKM). It is funded via the German Federation of Industrial Research Associations „Otto von Guericke“ (AiF) in the program for Industrial Collective Research (IGF), initiated by the Federal Ministry for Economic Affairs and Climate Action due to a resolution of the German Bundestag.