On-line slag composition analysis for electric arc furnaces
Summary
Electric steelmaking has fast gained ground in developed countries due to reduced CO2 emissions compared to blast furnace steelmaking and better production flexibility. Due to increased scrap usage, the quality of the scrap is getting worse and worse. This is reflected in the increase of non-metallic material in the scrap. Fluctuations in EAF scrap charge composition causes significant fluctuations in the EAF slag composition, since the non-metallic material in the scrap accumulates in the slag.
Fluctuation of slag composition causes many challenges in EAF steelmaking. In stainless steelmaking one of the most important goals in EAF is to keep the chromium content of the slag low, since it causes costs due to increased alloying additions and problems in recycling of slag. In carbon steelmaking it is important to ensure foaming slag conditions, which increases energy efficiency of the EAF. Due to the slag composition fluctuations the slag foaming is sometimes hindered when the slag composition drifts to the composition area with low foamability.
There are currently very few methods available for analysing slag composition in EAF. One of the most popular methods to gain information of slag composition is taking slag samples and analysing them in laboratory. Currently there is no method available to analyse slag composition in industrial EAFs on-line.
The objective of the proposal is the development of a continuous measurement system for EAF slag component analysis based on optical emission spectroscopy. The aim for stainless steel grades is the analysis of Cr2O3 and MnO content, while for carbon steel grades the aim is to analyse CaO, SiO2, Al2O3 and MgO content of the slag. The proposed technology will follow these criteria:
- remote and continuous measurement system for slag component analysis,
- low maintenance system design,
- optimized operating practices based on continuous slag composition data increasing resource and energy efficiency.
This project aims to develop a technology, which enables the online analysis of electric arc furnace and ladle furnace slag composition in EAF steelmaking. Currently there is no method available to analyse slag composition online in industrial electric arc furnaces in European or worldwide level. Better understanding of slag composition allows better control of the Cr2O3 content in stainless steelmaking, which reduces alloying and addition material costs. In carbon steelmaking the information of online slag composition makes it possible to optimise the slag composition in order to reduce metal losses, slag amount and refractory wear. Additional information on scrap melting and slag formation enables the better timing of carbon injection and increases energy efficiency.
Results achieved so far
In the first half of the project the activities were focused on the laboratory and pilot scale testing. The aim of these work packages was to provide fundamental understanding of arc emission spectra, define the optimal measurement system for industrial scale measurements and provide guidelines for correct measurement position and measurement practice for industrial scale. A preliminary result of the investigations in laboratory and pilot scale is that the main slag constituents CaO, SiO2, Al2O3, MgO and Cr2O3 can be measured with the new system with an average absolute accuracy between 0.1 and 1.9 wt-%. The accuracy estimate is preliminary and subject to change. The hardware and software development first lead to the early prototype used in laboratory and pilot scale and for a very first installation at a ladle furnace. This early prototype was designed to be located so that it would not be subjected to extreme temperatures and slag spray. The following design and development work on the advanced prototype was conducted with the aim of using the prototype to perform the first industrial testing at an EAF. The advanced prototype and especially the measurement head was redesigned to withstand extreme temperatures and slag spray, amongst other things by integrating an active slag removal system.
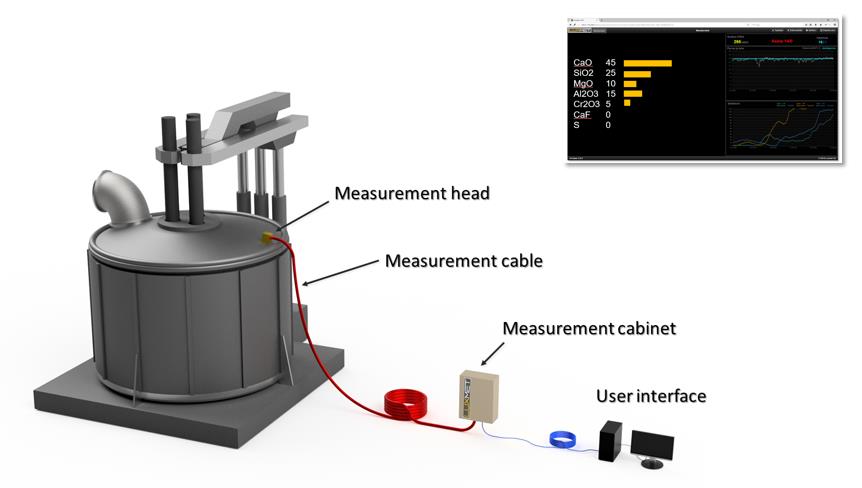
Schematic of the advanced prototype
The industrial testing at the ladle furnace started with a first installation of the early prototype at an LF. Measurement data was recorded for a period of six weeks, but unfortunately the quality of the measured spectra was not optimal. Only one of the three spectrometers measured good quality data. Industrial testing at the EAF for stainless steel grades has been prepared by planning of the EAF furnace roof adjustments needed at the participating steel plants for the installation of the measurement system. Installation of the modified roof/roof elements is delayed. The work on Industrial testing at the EAF for carbon steel grades is planned to start after the end of the first half of the project as scheduled.
Publications
Pauna, H.; Willms, T.; Aula, M.; Echterhof, T.; Fabritius, T.: Prospects of Plasma Analysis for Electric Arc Furnaces, 7th International Congress on Science and Technology of Steelmaking – ICS 2018, 13.–15. June 2018, Venice, Italy
This project receives funding from the Research Fund for Coal and Steel under grant agreement No 709923.