Cement-free brick production technology for the use of primary and secondary raw material fines in EAF steelmaking
Summary
Recent years have seen a world-wide change in the environmental policy towards integrated pollution prevention and control, taking into account all environmental media. It is estimated that steel-making activities in Europe produce about 80 million tonnes annually of by-products and waste, equivalent to half of the European steel production, of which more than 10 million tonnes is waste for disposal. This waste of resources and land area is not sustainable and has to be decreased in the future.
The Fines2EAF project aimed to increase the value of steelmaking residues by internal recycling and (re)use in the form of cement-free bricks. The benefit of this strategy is fourfold: improved utilization of residues, internal recovery of metals, reduction of the amount of dumped materials and saving of natural resources (e.g. limestone, dolomite and dolomitic lime). Through demonstration by operational tests the technology of cement-free bricks will become more acceptable for the steel works.
The approach followed was the development of an innovative process to produce cement-free bricks on the basis of primary and secondary raw material fines, alternative binder systems and a hydraulic stamp press. The bricks have to possess sufficient cold compression strength for low-abrasion handling and, for self-reducing bricks, sufficient reduction behaviour and metallurgical performance. To achieve these goals the fundamental understanding of the bricks, their manufacturing and their subsequent use in the EAF is necessary.
Project activities have developed methods, processes and solutions for:
- economic (re)using of low volume primary and secondary raw material fines in EAF steelmaking
- closing inter-sectoral material loops within the EAF steelmaking route by production of tailor-made high quality charge materials for the EAF
- recovery of metals in secondary raw material fines
- reducing the amount of waste materials, environmental impact and saving costs of (natural) raw materials.
The project was able to show that the production of cement-free bricks by stamp press is a valuable option to process a wide range of residue materials arising in lower amounts at the EAF steel plants in an economic way. It also contributes to a reduction of the use of primary materials, (indirect) CO2 emissions and needed landfill capacity.
Work performed and results achieved
In the first reporting period, the activities were focused on the sampling and characterization of materials and the lab investigations on pre-treatment and brick production. Residues from the steel plants and from suppliers and other industrial sectors were sampled and characterized. The physical and chemical characteristics of the materials were compiled in an inventory of primary and secondary raw materials. Data about amounts and current use of these materials were also included in the inventory. Based on the inventory, materials were selected for the work on the microwave pre-treatment process as well as for the recipe development and lab-scale brick production. A microwave pre-treatment to reduce the amount of materials like Zn, Pb and volatiles was investigated and compared to conventional furnace treatment. Results of the work could also show a different heating behaviour of the selected materials based on their composition. It could also be shown, that with the microwave heating a similar de-zincing of EAF dust could be reached at lower bulk temperature of the material and with a higher zinc purity of the removed dust. As part of the recipe development initially the priorities of the steel plants for the recipe development were defined based on the available materials and suitable use in the steel plant. The recipe development for Max Aicher Umwelt (MAU) und Marienhütte were focused on CaO and MgO containing materials to create synthetic slag former bricks. The recipe development for Sidenor focussed on the use of oxy-cutting fines, metallic iron containing grinding sludge and fines collected at the belt conveyors. Based on this selection a mechanical pre-treatment of the materials (crushing, sieving, etc.) was investigated where needed. In the lab-scale brick production different binders as well as different agglomeration parameters like pressing force, pressing time, drying conditions, etc were extensively tested. Bricks produced by a number of promising recipes were forwarded to the high-temperature testing.
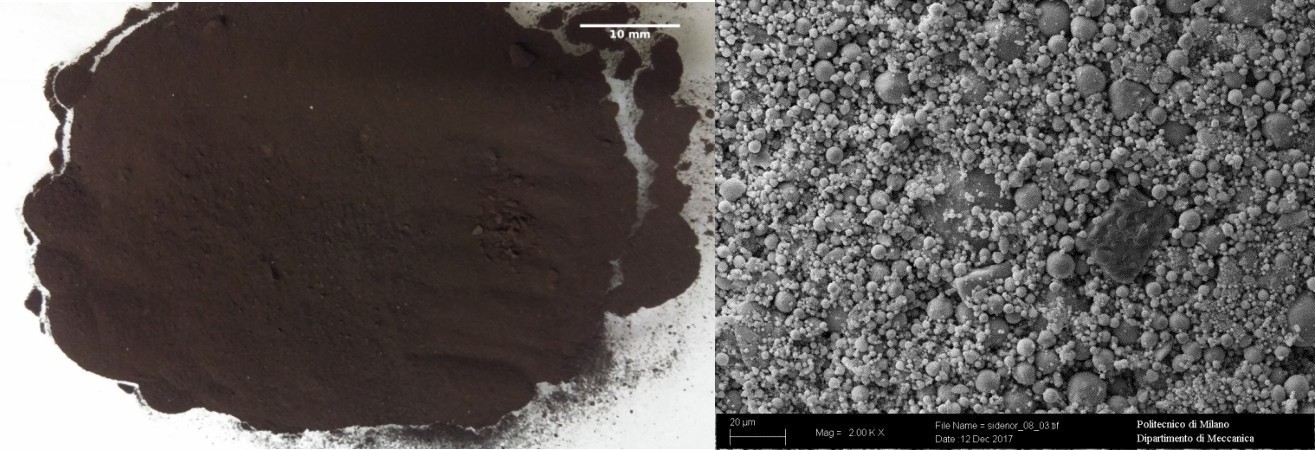
Oxy-cutting fines: picture (left) and SEM-SE micrography (right)
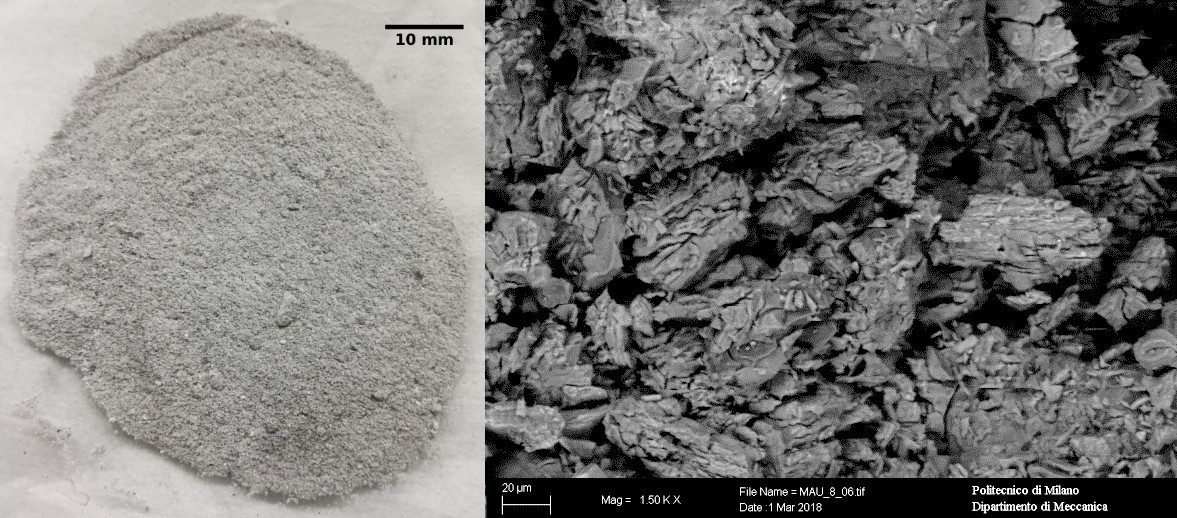
LF slag fines: picture (left) and SEM-SE micrography (right)
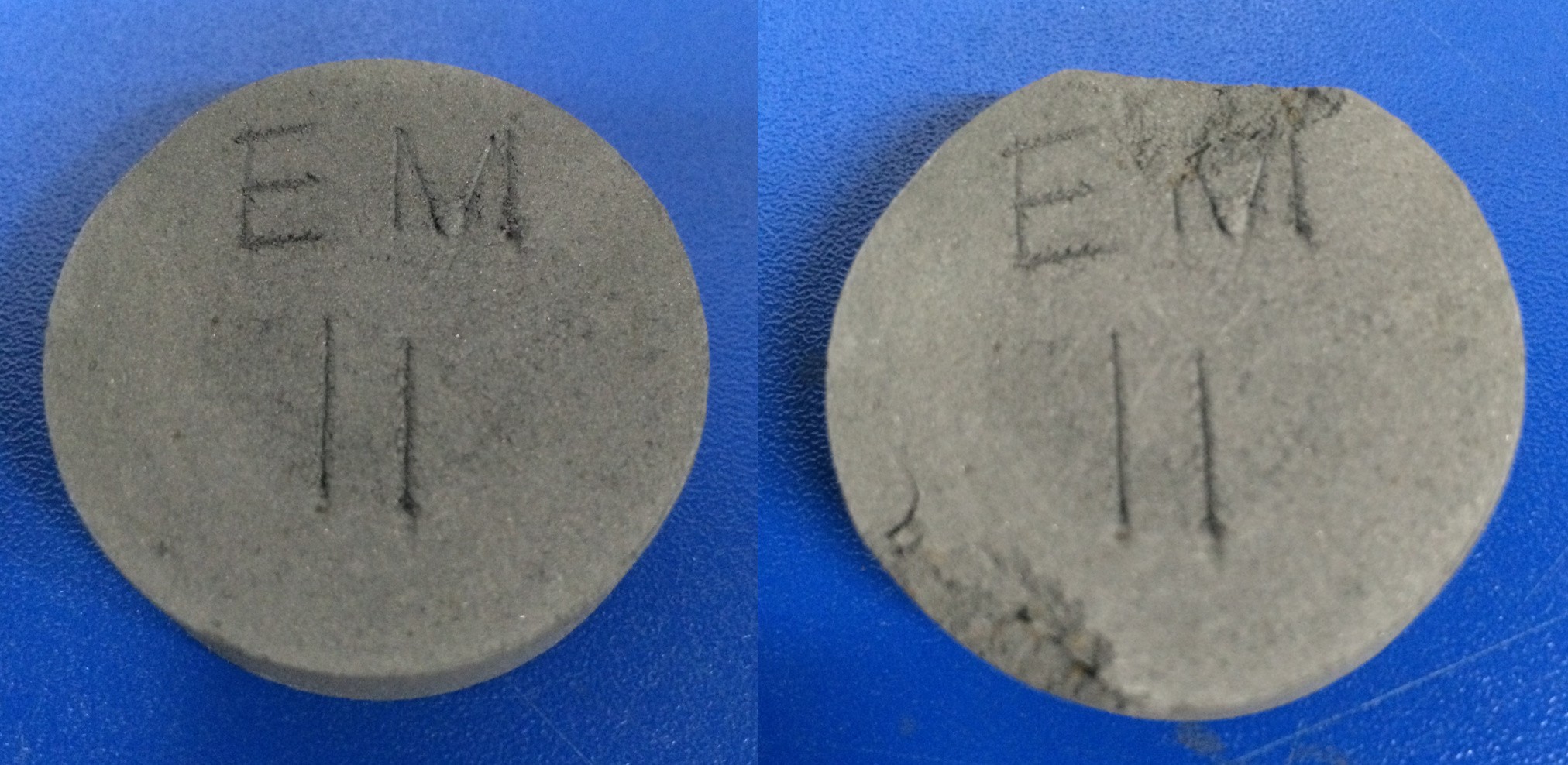
Agglomerated grinding sludge before (left) and after (right) drop test
During the second reporting period, the evaluation of the lab investigations on pre-treatment and the lab-scale brick production and evaluation were finalized. The activities were focused on the high-temperature testing of the bricks, the pilot-scale brick production and the industrial testing. The project was concluded by the techno-economical evaluation. The evaluation and reporting on the lab investigation of microwave pre-treatment of the selected materials was finalized. Also, the physical evaluation of recipes was finalized and bricks produced in the lab were delivered to the responsible partners for high temperature testing. The determination of the thermal behaviour of the produced bricks was investigated by optical dilatometry, by TGA-MS, by melting and dissolution trials up to technical scale melting experiments etc. The work was mainly conducted by POLIMI, Montanuniversität Leoben (MUL) and University of Oulu and finalized by an evaluation of the metallurgical performance of the tested recipes. Based on the results of the lab-scale brick production and evaluation and the high-temperature testing of the bricks final recipes for pilot-scale brick production were defined. The pilot-scale brick production was set up at and conducted mainly by MFG. Material from the MAU and Marienhütte steel plants was delivered to MFG for brick production, while transportation of Sidenor material was in part not possible due to national regulations. Sidenor commissioned a national company to produce the bricks for industrial testing. Overall about 81 t of bricks were produced in Germany and Spain and delivered to the steel plants and final recipes were defined during brick production. The following industrial testing were conducted at the EAFs of the partners MAU, Marienhütte and Sidenor and included also an extensive investigation on the influence of the brick use on the quality of the EAF slag. The steel plants conducted in total 7 trial campaigns with 66 heats. These industrial trials could show, that the use of cement-free residue bricks can substitute the use of lime/dololime but also recover iron without any negative influence on furnace operation, steel or slag quality. The project was concluded by a techno-economical as well as an ecological evaluation and dissemination activities. The technical and economical evaluation included the development of plant concepts for a brick production with and without pre-processing of the residues. The overall costs of brick production calculated are in the range of about 60 to 105 EUR/t brick. This range is mainly based on the need for pre-processing and the amount and cost of used binder. These costs are offset by the costs for primary lime/dololime and landfilling that are saved by the use of this technology. The ecological evaluation was based on a life cycle analysis, which compared the current reference practice with a practice substituting slag formers and substituting scrap in both cases reducing the need for landfilling. The substitution of burned lime by recycled slag formers showed a higher reduction of the global warming potential than the substitution of scrap by metal bearing residues. Dissemination activities of the project included a number of publications, theses and the organisation of a dedicated workshop on the “(Re)use of primary and secondary raw material fines in the EAF”. Furthermore, at one of the involved steel plants the advanced planning of a new area for storing and handling of the residues and for residue brick production is ongoing at the end of the project.
Progress beyond the state of the art and potential impacts
This project aimed at the (re)use of primary and secondary raw material fines in EAF steelmaking and conservation of resources by development of cement-free brick production technology, to be applied directly inside the steel plant. The development of the technology brings the following advantages: avoid disposal of wastes, enhance the use of primary raw material fines and the recycling of secondary raw material fines for steel production, save costs by substituting primary raw materials like lime/dololime and iron, and reduce the environmental impact of the steel plant on the surrounding again by reduction of landfilling and an improved carbon footprint of the steel production.
Publications
Echterhof, T.; Willms, T.; Preiß, S.; Omran, M; Fabritius, T.; Mombelli, D.; Mapelli, C.; Steinlechner, S.; Unamuno, I.; Schüler, S.; Mudersbach, D.; Griessacher, T.: Developing a new process to agglomerate secondary raw material fines for recycling in the electric arc furnace – the Fines2EAF project, CLEAN TECH 4 — The 4th European Conference on Clean Technologies in the Steel Industry, 28.–29. November 2018, Bergamo, Italy
Echterhof, T.; Willms, T.; Preiß, S.; Omran, M; Fabritius, T.; Mombelli, D.; Mapelli, C.; Steinlechner, S.; Unamuno, I.; Schüler, S.; Mudersbach, D.; Griessacher, T.: Developing a new process to agglomerate secondary raw material fines for recycling in the electric arc furnace – the Fines2EAF project, La Metallurgia Italiana, 111 (2019), Nr. 5, S. 31–40
Echterhof, T.; Willms, T.; Preiß, S.; Aula, M.; Abdelrahim, A.; Fabritius, T.; Mombelli, D.; Mapelli, C.; Steinlechner, S.; Unamuno, I.: Fabrication of Agglomerates from Secondary Raw Materials Reinforced with Paper Fibres by Stamp Pressing Process, Applied Sciences, 9 (2019), 3946
Willms, T.; Echterhof, T.; Steinlechner, S.; Aula, M.; Abdelrahim, A.; Fabritius, T.; Mombelli, D.; Mapelli, C.; Preiss, S.: Investigation on the Chemical and Thermal Behavior of Recycling Agglomerates from EAF by-Products, Applied Sciences, 10 (2020), 8309
Abdelrahim, A.; Aula, M.; Iljana, M.; Willms, T.; Echterhof, T.; Steinlechner, S.; Mombelli, D.; Mapelli, C.; Omran, M.; Preiss, S.; Fabritius, T.: Suitability of Self-Reducing and Slag-Forming Briquettes for Electric Arc Furnace Use Based on Laboratory Tests, steel research international, 2100472
This project received funding from the Research Fund for Coal and Steel under grant agreement No 754197.