EnabEL: Sustainable electrification of thermal processing plants — Technological enablers for the large-scale industrial use of resistance heating
Industrial Collective Research (IGF), 1 November 2023 — 30 April 2026
Project description
As part of the energy transformation, a reduction in CO2 emissions is essential in thermal process technology too. In addition to optimising the heating systems currently used, which are based on fossil fuels, this requires above all a transformation to alternative concepts. Electric heating systems are one option for CO2-neutral heating, provided that no fossil fuels are used to generate the electricity. In the field of process heat generation, however, these electric heating systems are currently only available in small numbers or limited to special applications (e.g. electric arc furnaces). Resistance heating in particular offers the possibility of being used in a wide range of systems. At present, there are still several questions regarding the widespread use of resistance heating. The “Sustainable electrification of thermal processing plants — EnabEL” project pursues the overarching objective of expanding the range of electrification of thermal processing plants (industrial furnaces) through resistance heating. Overall, the project is made up of the three closely interlinked sub-projects “HighPowHeat”, “OptiELHeat” and “MatELHeat” and focuses primarily on expanding the scope of application of resistance heating systems in plants with plant power capacities of generally < 1 MW to date to power capacities of up to 10 MW or more.
Sub-project 1: HighPowHeat — Feasibility studies for high electrical connected loads in thermal processing plants with resistance heating
Sub-project 2: OptiELHeat — Optimised thermal design of powerful electrical resistance heating systems for convection-dominated thermal processing plants
Sub-project 3: MatELHeat — Investigations into the material-technical design of electrical resistance heating systems for hybrid-heated thermal processing plants
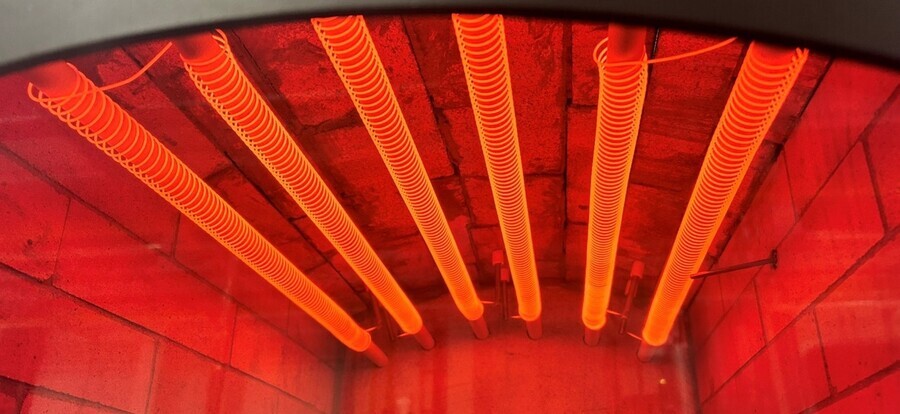
Resistance heating elements in a furnace
As already described, the coverage of this extended output range is necessary for the objectives of the energy transformation. Plants that are characterised by low outputs, a less complex structure, simple process control requirements, no flue gas system and short operating times per year are already electrified. In contrast, large industrial plants are characterised by significantly higher installed electrical outputs and long annual operating times. This results in requirements for resistance-based heating element systems for use in extended power ranges (e.g. power input, operating time, H2-rich atmospheres), which must be intensively investigated. One example of this is the overheating of the individual heating elements. Localised overheating often leads to premature failure of the elements and should therefore be avoided wherever possible. For this reason, the electrical energy supply and the subsequent heat exchange via the surface of the elements are being investigated in the “HighPowHeat” and “OptiELHeat” sub-projects. At the same time, overheating and the resulting local rise in temperature also leads to increasing oxidation of the heating element materials. This in turn leads to damage to the elements. The effects of the temperatures and atmospheres on the materials of the heating elements are being investigated in the “MatELHeat” sub-project.
Given this background, the aspect of longer usability of the elements plays a decisive role in the three sub-projects of the lead technology project, alongside an increase in performance. These objectives cannot be investigated and realised independently of each other, but require a holistic view of
- the power supply and power electronics of the heating elements with higher voltages as well as the options of a supply with alternating voltage (AC) or direct voltage (DC) (sub-project 1, HighPowHeat),
- the thermo-/electrical design of the heating element systems or hot gas generators integrated into the furnaces (sub-project 2, OptiELHeat) as well as
- the service life of heating element materials for purely electric, but also for hybrid operation (combined electric/fossil operation as a bridging technology or later H2/electricity) (sub-project 3, MatELHeat).
The knowledge gained in the lead technology project will be summarised in a joint guideline at the end of the projects in order to enable an improved design and optimised operation of the heating elements and thus expand the possible applications in thermal process technology.
Project goals
- Expansion of the application range of electric resistance heating systems
- Increasing the power input of the heating elements into the systems through new concepts in the field of electrical actuation
- Optimisation of heat transfer between heating elements and furnace atmosphere using experimental and numerical methods
- Improving the material design on the basis of ageing tests and damage models
- Creation of a guideline for the optimised design of resistance heating elements
Project participants
Sub-project 1 “HighPowHeat”:
Institut für Industrieofenbau und Wärmetechnik (IOB), RWTH Aachen
Kopernikusstr. 10, 52074 Aachen
Institut für Stromrichtertechnik und Elektrische Antriebe (ISEA), RWTH Aachen
Campus-Boulevard 89, 52074 Aachen
Institut für Elektroprozesstechnik (ETP), Leibniz Universität Hannover
Wilhelm-Busch-Str. 4, 30167 Hannover
Sub-project 2 “OptiELHeat”:
Institut für Industrieofenbau und Wärmetechnik (IOB), RWTH Aachen
Kopernikusstr. 10, 52074 Aachen
Lehrstuhl f. Gas- und Wärmetechnische Anlagen (GWA), TU Bergakademie Freiberg
Gustav-Zeuner-Str. 7, 09599 Freiberg
Sub-project 3 “MatELHeat”:
OWI Science for Fuels gGmbH (OWI), An-Institut der RWTH Aachen
Kaiserstraße 100, 52134 Herzogenrath
DECHEMA-Forschungsinstitut
Theodor-Heuss-Allee 25, 60486 Frankfurt am Main
Contact
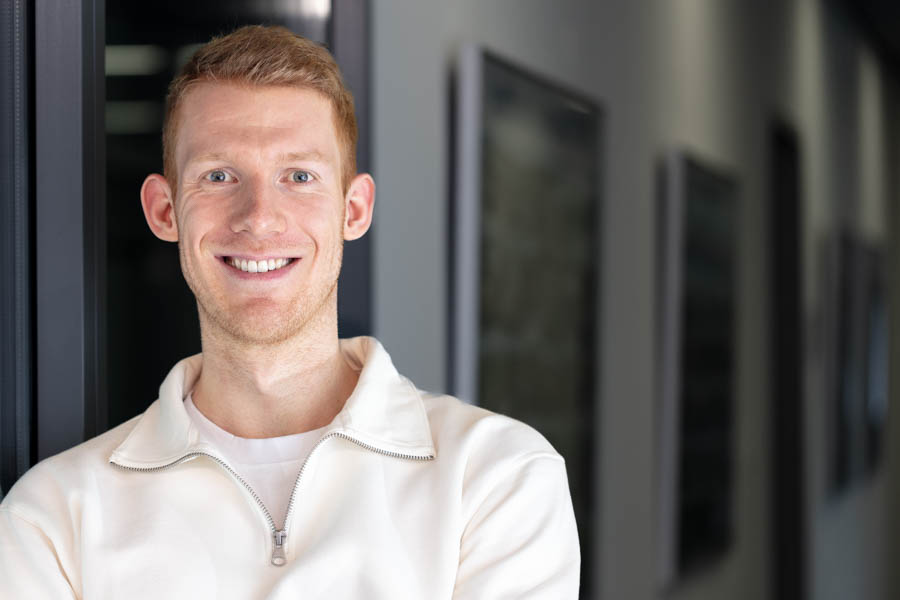
Julius Wilker, M.Sc.
+49 241 80–25965
Dr.-Ing. Dominik Büschgens
+49 241 80–26067
Funding
The lead technology project with the individual projects “HighPowHeat” (project no. 01IF00066E), “OptiELHeat” (project no. 01IF00067E) and “MatELHeat” (project no. 01IF00068E) was submitted with the support of the Forschungsgemeinschaft Industrieofenbau e.V. (FOGI) and the DECHEMA Gesellschaft für Chemische Technik und Biotechnologie e. V. (DECHEMA) via the Forschungskuratorium Maschinenbau e.V. (FKM). It is financially supported by the German Aerospace Center (DLR) in the program for the Promotion of Industrial Research (IGF), initiated by the Federal Ministry for Economic Affairs and Climate Action due to a resolution of the German Bundestag.